
10 Essential Steel Grades Explained
Table of Contents
Introduction
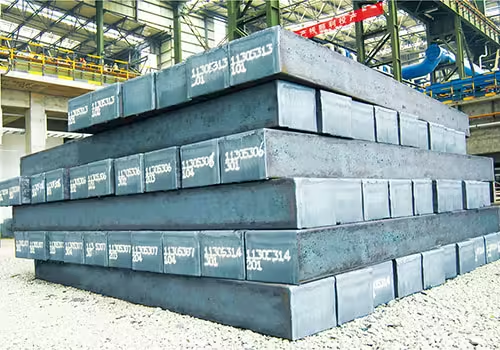
Steel is one of the most vital materials in modern industry. It is used in construction, automotive manufacturing, energy infrastructure, appliances, tools, and countless other sectors. The versatility, strength, and affordability of steel make it an irreplaceable component of both everyday life and industrial development.
However, not all is the same. The performance of steel depends significantly on its chemical composition, mechanical properties, and heat treatment. This is why different steel grades exist. These grades are standardized categorizations that help engineers, designers, and procurement specialists select the right material for their specific application.
In this blog, we will explain 10 essential steel grades that are widely used across industries. Each grade is tailored for certain performance characteristics, including hardness, corrosion resistance, tensile strength, and formability. Whether you’re involved in heavy manufacturing, precision engineering, or construction, understanding these steel grades is essential to ensure safety, efficiency, and cost-effectiveness.
Understanding Steel Grade Classifications
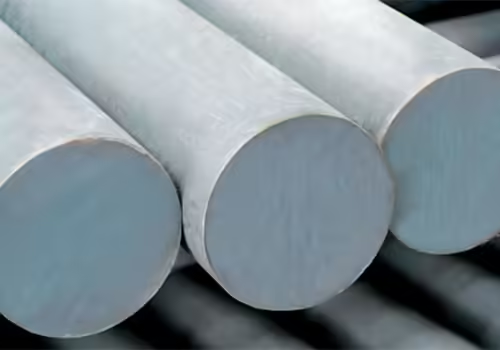
Steel grades are assigned by recognized standards organizations such as ASTM (American Society for Testing and Materials), SAE (Society of Automotive Engineers), and EN (European Norm). Each system uses different criteria to classify steel, usually based on its chemical composition and intended use.
For instance:
- ASTM A36 is a common structural steel grade used in construction.
- SAE 1045 is a medium-carbon steel known for strength and impact resistance.
- 304 Stainless Steel is widely used for corrosion-resistant applications.
Before we dive into the 10 essential steel grades, here’s a brief overview of how they are generally categorized:
- Carbon Steel: Low, medium, or high carbon content.
- Alloy Steel: Steel mixed with elements like chromium, molybdenum, or nickel.
- Stainless Steel: Contains high levels of chromium and offers corrosion resistance.
- Tool Steel: Designed for high hardness and wear resistance.
The Table of 10 Essential Steel Grades
Steel Grade | Type | Key Features | Common Applications |
---|---|---|---|
ASTM A36 | Carbon Steel | Affordable, easy to weld, good machinability | Construction, bridges, structural parts |
SAE 1045 | Carbon Steel | Medium strength, good wear resistance | Shafts, gears, axles |
AISI 1018 | Carbon Steel | High ductility, good weldability | Machinery components, fasteners |
4140 | Alloy Steel | High fatigue strength, tough | Aerospace, automotive, oil & gas |
8620 | Alloy Steel | Excellent carburizing properties | Gears, crankshafts, heavy-duty machines |
304 | Stainless Steel | Corrosion-resistant, non-magnetic | Food industry, kitchen equipment |
316 | Stainless Steel | High corrosion resistance, marine-grade | Chemical processing, marine applications |
D2 | Tool Steel | High hardness, wear-resistant | Cutting tools, dies, punches |
H13 | Tool Steel | High toughness, heat-resistant | Injection molds, hot work tooling |
17-4 PH | Stainless Steel | High strength, corrosion-resistant | Aerospace, nuclear reactors, valves |
Grade 1: ASTM A36 – The Workhorse of Structural Applications
ASTM A36 is a low-carbon steel grade that is easy to machine, weld, and fabricate. It is one of the most commonly used structural steels due to its good balance of strength and ductility.
Key Properties:
- Tensile strength: 400-550 MPa
- Yield strength: 250 MPa
- Elongation: 20% minimum
Ideal for buildings, bridges, and general structural projects, ASTM A36 is a go-to material where strength and economy are essential.
Grade 2: SAE 1045 – The Tough Medium-Carbon Steel
SAE 1045 is a versatile steel that offers higher strength than low-carbon steel grades. It is often chosen for parts that need higher wear resistance and tensile strength.
Key Properties:
- Good impact resistance
- Better machinability than high-carbon steel
It is commonly found in drive shafts, gears, bolts, crankshafts, and a variety of industrial components that demand durability and performance under stress. This grade balances cost and strength, making it suitable for both automotive and general engineering applications.
Grade 3: AISI 1018 – Easy to Weld and Machine
AISI 1018 is a low-carbon steel with excellent weldability and formability. It’s commonly used in manufacturing operations where bending, machining, and welding are required.
Benefits:
- Uniformity in chemical composition
- Smooth surface finish
Its relatively low carbon content and ease of manipulation make it ideal for producing precision parts, such as pins, rods, spindles, and other components that require consistent machining characteristics. It’s also frequently used in applications where aesthetic finish is important.
Grade 4: 4140 – A High-Performance Alloy Steel
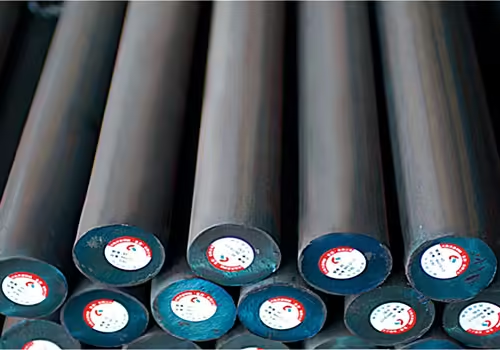
4140 alloy steel offers a great combination of strength, hardness, and resistance to fatigue. It’s widely used in industries where components are exposed to dynamic loads.
Features:
- Contains chromium and molybdenum
- Can be heat-treated for increased hardness
This grade is particularly favored in aerospace and automotive industries for making critical load-bearing parts such as axles, drill collars, gear shafts, and structural tubing. Its fatigue resistance and toughness make it reliable in heavy-duty settings.
Grade 5: 8620 – The Best for Carburizing
8620 steel is a case-hardening alloy steel, ideal for parts that require a tough core and wear-resistant surface. It’s commonly 8620 steel is a case-hardening alloy steel, ideal for parts that require a tough core and wear-resistant surface. It’s commonly used in gear systems and other high-load applications.
Highlights:
- Excellent toughness
- Good core strength
Its capability to undergo carburizing makes it the steel of choice for components like heavy-duty transmission parts, crankshafts, and industrial gearing systems. The carburized outer shell significantly extends component life under wear and friction.
Grade 6: 304 Stainless – Universal Corrosion Resistance
304 stainless steel is one of the most widely used stainless steel grades. Its excellent corrosion resistance makes it suitable for a wide range of applications.
Attributes:
- Non-magnetic in annealed condition
- Excellent formability and cleanability
304 is used extensively in environments requiring hygiene and cleanliness such as food processing, chemical containers, kitchen equipment, and architectural structures. It is easy to clean and maintain.
Grade 7: 316 Stainless – The Marine-Grade Steel
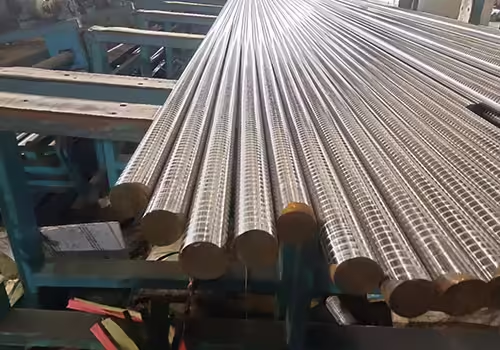
316 stainless steel includes molybdenum, enhancing its corrosion resistance, especially in marine and chemical 316 stainless steel includes molybdenum, enhancing its corrosion resistance, especially in marine and chemical environments.
Advantages:
- Superior resistance to chlorides and acids
- High-temperature strength
This grade is essential in applications involving exposure to seawater, acidic compounds, or other harsh conditions. It is widely used in boat fittings, surgical tools, and chemical processing equipment.
Grade 8: D2 Tool Steel – Built to Cut
D2 is a high-carbon, high-chromium tool steel that provides extreme wear resistance and hardness.
Primary Benefits:
- Excellent dimensional stability
- High compressive strength
D2 is ideal for tools and dies that perform cutting, shearing, or punching operations. It maintains sharp edges under high pressure, making it indispensable in toolmaking and metal fabrication industries.
Steel Grade 9: H13 Tool Steel – Heat and Pressure Tough
H13 is a chromium-molybdenum tool steel known for high hot-wear resistance and thermal fatigue strength.
Key Characteristics:
- Excellent toughness
- High thermal shock resistance
This steel grade is used for hot forging dies, aluminum die casting molds, extrusion tooling, and plastic injection molds. It maintains strength under high heat and pressure cycles.
Grade 10: 17-4 PH – The Stainless Powerhouse
17-4 PH is a precipitation-hardened stainless steel with high strength and excellent corrosion resistance. It maintains properties even at high temperatures.
Strong Points:
- Hardens quickly with low distortion
- Maintains strength up to 600°F
It’s a top choice in aerospace, nuclear, and petrochemical industries. Applications include turbine blades, nuclear reactor components, and valves that require both strength and corrosion resistance.
Conclusion
Understanding the properties and advantages of different steel grades is crucial for making informed material choices. Whether you need strength, machinability, corrosion resistance, or wear performance, there’s a steel grade engineered to meet your needs.
These 10 essential steel grades cover a broad spectrum of applications, from basic structural use to high-performance aerospace systems. By selecting the correct grade, you not only improve functionality but also increase safety, extend service life, and reduce operational costs.
FAQ
What is the most commonly used steel grade?
Among the numerous material types used across industries, ASTM A36 stands out as one of the most popular. Its widespread adoption can be attributed to its excellent balance of cost and performance. This particular option is highly favored in structural applications because it’s not only affordable but also offers good weldability and machinability, making it an ideal choice for construction and general fabrication. Thanks to its versatility, it’s often considered the benchmark for general-purpose structural materials.
What makes stainless steel different from carbon steel?
The primary difference lies in composition. Stainless variants contain a significant amount of chromium—typically above 10.5%—which forms a passive layer that resists oxidation and corrosion. On the other hand, carbon-based materials prioritize strength and hardness, relying more heavily on carbon content to achieve desired mechanical properties. As a result, stainless types are commonly used in environments prone to moisture or chemical exposure, whereas carbon options excel in applications demanding rigidity and wear resistance. The added chromium content in stainless grades also enhances longevity, making them a frequent choice in food processing, medical, and marine industries.
Is alloy steel stronger than carbon steel?
In most cases, yes. Materials categorized as alloyed are specifically engineered for enhanced mechanical characteristics. They incorporate additional elements such as chromium, molybdenum, and nickel, which contribute to superior tensile strength, improved toughness, and better fatigue resistance. These enhancements make them suitable for high-performance applications like aerospace components and heavy-duty machinery. While standard carbon materials are strong in their own right, they generally do not match the durability and versatility of these enhanced alternatives. Alloyed variants offer better consistency in demanding environments, particularly where heat and stress are constant factors.
Can I weld all types of steel grades?
Welding compatibility varies depending on the specific material and its chemical makeup. Many commonly used low-carbon varieties, such as AISI 1018, are particularly well-suited for welding and require minimal preparation. However, tool-oriented options like D2 often present challenges due to their higher hardness and alloy content, which may necessitate special techniques or preheating. Understanding the composition of the material being used is essential to achieving clean, strong welds and avoiding structural weaknesses. Professionals often rely on welding charts and metallurgy knowledge to match the correct procedure to each type.
Why is it important to choose the right steel grade?
Selecting the appropriate composition is essential for ensuring that a project meets its intended performance, safety, and durability standards. The right match can lead to better mechanical efficiency, extended service life, and reduced maintenance or replacement costs. Conversely, a poor choice might compromise structural integrity or lead to unexpected failures. Tailoring the material to its specific function and environment is key to maximizing both short-term functionality and long-term value. Making informed decisions during the design phase can prevent costly errors later in the project lifecycle.