
1018 vs 1020 Cold Rolled Steel: 5 Critical Differences
Table of Contents
Introduction
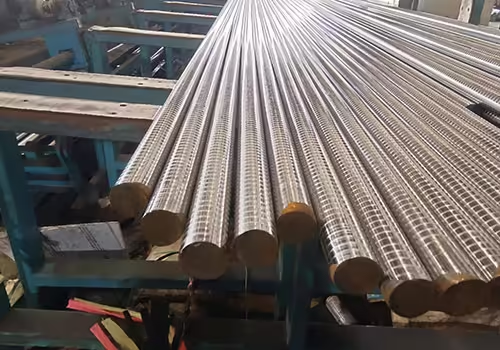
When selecting steel materials for fabrication or manufacturing, understanding the properties of different grades is crucial. Among the commonly used options, 1018 vs 1020 Cold Rolled Steel often comes into comparison due to their similar appearance and overlapping applications. However, subtle differences in composition, mechanical properties, and formability make each grade suitable for specific uses.
In this comprehensive guide, we will explore the critical differences between 1018 vs 1020 Cold Rolled Steel. By delving into their chemical composition, mechanical characteristics, machinability, and usage scenarios, we aim to provide a clearer understanding of 1018 vs 1020 Cold Rolled Steel. This will help clarify the key distinctions and assist you in making an informed decision about which grade is best suited for your next project involving 1018 vs 1020 Cold Rolled Steel.
Chemical Composition Comparison of 1018 vs 1020 Cold Rolled Steel
Although 1018 and 1020 cold rolled steel belong to the same carbon steel family, they have distinct chemical compositions. This difference in carbon content plays a major role in determining their properties. Here is a detailed breakdown:
Table: Chemical Composition of 1018 vs 1020 Cold Rolled Steel
Element | 1018 Cold Rolled Steel | 1020 Cold Rolled Steel |
---|---|---|
Carbon (C) | 0.15% – 0.20% | 0.18% – 0.23% |
Manganese (Mn) | 0.60% – 0.90% | 0.30% – 0.60% |
Phosphorus (P) | Max 0.04% | Max 0.04% |
Sulfur (S) | Max 0.05% | Max 0.05% |
As shown in the table, the slightly higher carbon content in 1020 gives it greater strength and hardness compared to 1018. However, 1018 offers better machinability due to its lower carbon content.
Mechanical Properties of 1018 vs 1020 Cold Rolled Steel
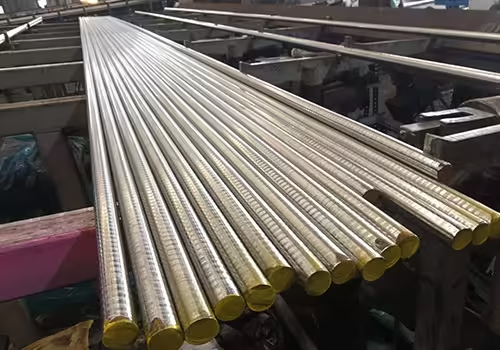
Understanding mechanical behavior is essential for applications that involve stress, impact, and load-bearing requirements. While both 1018 and 1020 are categorized as low-carbon steels, slight differences in composition contribute to unique mechanical characteristics that affect their performance in practical use.
Tensile Strength and Yield Strength
1018 cold rolled steel typically exhibits a tensile strength of approximately 440 MPa and a yield strength around 370 MPa. These values make it a solid choice for general-purpose engineering tasks where moderate strength and excellent machinability are needed.
In contrast, 1020 cold rolled steel generally provides a tensile strength near 420 MPa and a yield strength around 350 MPa. While these figures are slightly lower than those of 1018, 1020 still offers sufficient strength for many structural and mechanical applications. The difference is minimal but can be significant depending on project requirements.
Hardness and Toughness
1020 steel tends to have slightly higher hardness due to its increased carbon content. This additional hardness improves wear resistance, making it better suited for parts subject to friction and repetitive motion. However, with increased hardness comes a slight trade-off in ductility.
1018, on the other hand, maintains a balance between strength and ductility. Its softer composition makes it easier to form and deform without cracking, which is especially beneficial for components that require bending, shaping, or high levels of precision.
Machinability and Weldability: 1018 vs 1020 Cold Rolled Steel
Both 1018 and 1020 cold rolled steels are known for favorable machinability and weldability. However, their slight differences affect how they perform in fabrication and processing.
Machinability of 1018 is superior among mild steels. Its low carbon content allows cutting tools to pass through with less resistance, reducing tool wear and enabling fine surface finishes. As a result, it is widely used in precision machining, particularly in components that require tight tolerances.
1020 is also machinable, but its higher carbon content increases tool wear and may necessitate slower machining speeds or more robust tooling. This makes it more suitable for parts where strength is more critical than high-precision machining.
Weldability is strong for both steel types. Neither 1018 nor 1020 generally requires preheating before welding, and both can be welded using standard methods such as MIG, TIG, and arc welding. However, 1018 may be slightly easier to weld cleanly due to its softer composition, which reduces the risk of cracking or distortion during the welding process.
Formability is another area where 1018 excels. Its high ductility means it can be easily bent, formed, or rolled without compromising its structural integrity. 1020 can also be formed but may require slightly more force or heat treatment to achieve similar results.
Applications and Use Cases of 1018 vs 1020 Cold Rolled Steel
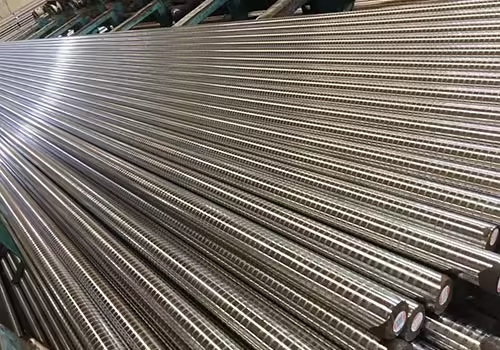
The specific advantages of each steel grade make them suitable for different industrial applications. Choosing between 1018 and 1020 often comes down to evaluating the demands of the intended use.
Common Applications of 1018 Cold Rolled Steel
1018 is frequently used in projects that demand high machinability and excellent surface finish. It’s ideal for components that require intricate cutting, shaping, and detailing. Examples include:
- Precision components such as pins, dowels, and shafts
- Gears, sprockets, and ratchets that benefit from tight tolerances
- Furniture hardware and brackets requiring smooth finishes
- Machine parts where ease of fabrication is prioritized
The consistent mechanical properties of 1018 make it a favorite in manufacturing environments that value repeatability and ease of modification.
Common Applications of 1020 Cold Rolled Steel
1020 is often selected for projects where strength, wear resistance, and durability are more important than machinability. Its higher carbon content enhances its ability to withstand physical stress, making it suitable for:
- Automotive components such as axles, crankshafts, and bushings
- Tubular products and structural shapes used in construction
- Mechanical parts in machinery that endure repetitive motion or heavy loads
- Agricultural equipment requiring higher strength and impact resistance
Thanks to its balance of strength and workability, 1020 serves well in applications that involve moderate forming and welding while still needing increased load-bearing capacity.
Cost and Availability: A Practical Comparison
When evaluating materials for engineering or manufacturing projects, cost and availability are major considerations. Comparing 1018 vs 1020 Cold Rolled Steel, the choice is often influenced not only by mechanical performance but also by pricing, accessibility, and consistency in supply.
Price Point
In terms of pricing, 1018 cold rolled steel typically enjoys a lower cost per unit due to its widespread use and high demand in the market. Its excellent machinability and formability make it a popular option across various industries, which in turn contributes to economies of scale in production and distribution. As a result, users frequently find 1018 to be the more budget-friendly choice when deciding between 1018 vs 1020 Cold Rolled Steel.
1020 cold rolled steel, on the other hand, may be marginally more expensive. This is often attributed to its enhanced mechanical properties, including slightly higher hardness and strength. Although the price difference is not dramatic, it can become more noticeable in large-scale orders or applications requiring specialized processing.
That said, the price disparity between 1018 vs 1020 Cold Rolled Steel is usually small enough that performance and application-specific needs will outweigh cost concerns in most scenarios.
Supply Considerations
Both 1018 and 1020 cold rolled steel grades are commonly stocked by major steel suppliers and distributors, making them easy to source in standard dimensions and quantities. However, 1018 cold rolled steel tends to have broader inventory availability due to its widespread use in precision machining, automotive parts, and general manufacturing.
In high-volume production environments where maintaining consistency across batches is essential, 1018 cold rolled steel offers a slight edge. Its predictable performance characteristics and uniformity make it ideal for automated processes or mass production lines.
Meanwhile, 1020 cold rolled steel may require more careful planning when ordering in bulk or custom sizes, especially for specialized applications. Nonetheless, both options remain viable and accessible for most industrial users.
Environmental and Long-Term Performance Differences
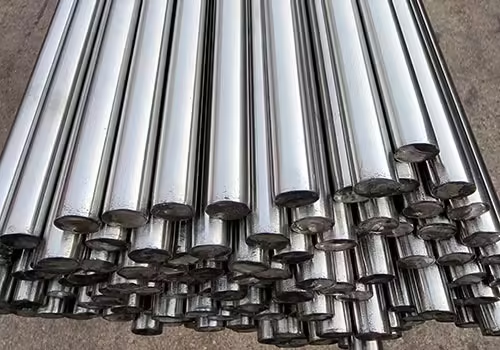
Beyond cost and availability, it’s important to consider how 1018 vs 1020 Cold Rolled Steel behave over time and under various environmental conditions. Longevity, resistance to fatigue, and environmental resilience are crucial factors, particularly for structural or outdoor applications.
Corrosion Resistance
Neither 1018 nor 1020 cold rolled steel offers inherent corrosion resistance. As low-carbon steels without alloying elements like chromium or nickel, they are susceptible to rust and oxidation when exposed to moisture or corrosive environments.
For projects where exposure to water, chemicals, or outdoor elements is expected, both 1018 and 1020 cold rolled steel require protective measures. These may include:
- Galvanizing or zinc coating
- Powder coating or painting
- Oil or wax treatments
- Use of corrosion inhibitors during storage or shipping
Choosing between 1018 vs 1020 Cold Rolled Steel in this context often depends on how the material will be treated post-fabrication. If corrosion resistance is a top priority, either steel type must be paired with appropriate surface treatments to extend service life.
Fatigue Resistance
When evaluating 1018 vs 1020 Cold Rolled Steel in terms of fatigue resistance, 1020 steel has a slight advantage. Its higher carbon content contributes to greater hardness and resistance to micro-fracturing over repeated stress cycles. This makes it more suitable for components subjected to vibration, torsion, or high-frequency load fluctuations.
However, both steel types can suffer from fatigue failure if not properly maintained or designed with stress relief features. Regular inspection and routine maintenance are essential, especially in load-bearing or dynamic systems.
Ultimately, while 1020 cold rolled steel may perform slightly better in cyclic loading environments, 1018 steel remains an excellent choice where fatigue is not the primary concern.
Conclusion
Deciding between 1018 vs 1020 cold rolled steel involves evaluating chemical composition, mechanical characteristics, workability, and application needs. 1018 offers excellent machinability and is ideal for high-precision parts, while 1020 provides better strength and hardness for demanding structural uses.
By analyzing the critical differences discussed in this guide, you can align your material choice with the performance requirements of your specific project.
FAQ
What is the main difference between 1018 and 1020 cold rolled steel?
The primary difference lies in carbon content. 1018 has slightly lower carbon content, offering better machinability, while 1020 has higher strength and hardness.
Is 1018 or 1020 better for welding?
Both have excellent weldability, but 1018 is slightly easier to work with due to lower carbon content.
Which steel is cheaper, 1018 or 1020?
Generally, 1018 is more affordable and more readily available.
Can I use 1020 instead of 1018 for precision machining?
You can, but 1018 is preferred for its higher machinability, especially in precision applications.
Are 1018 and 1020 interchangeable?
Not entirely. They can be used for similar purposes, but their specific properties may make one more suitable than the other depending on the application.