
1020 Steel vs A36: Key Differences Explained
In the world of structural steel, choosing the right material for your project is crucial. Two of the most common types of carbon steels used in construction and manufacturing are 1020 steel and A36 steel. While both are widely used, they offer different properties that make them suitable for different applications. This comprehensive guide will break down the key differences between 1020 steel vs A36, helping you understand which material is the best choice for your specific needs.
Table of Contents
Introduction
When it comes to choosing steel for manufacturing or construction, 1020 steel vs A36 is a frequently discussed comparison. Both steels are considered mild carbon steels, but they have distinct properties that influence their suitability for different tasks. Whether you’re designing structural components, manufacturing machine parts, or engaging in welding projects, understanding the differences between 1020 steel vs A36 can help you make an informed decision.
In this article, we’ll explore the composition, mechanical properties, applications, and welding considerations of these two steels to guide you in making the best material selection for your needs.
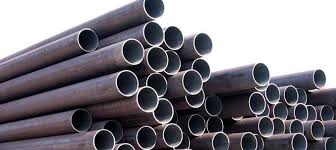
What is 1020 Steel?
1020 steel is a low-carbon steel that contains approximately 0.18% to 0.23% carbon content, which makes it relatively soft and easy to machine. It is known for its high tensile strength and ductility, making it ideal for various applications that require a balance of strength and workability.
Some important characteristics of 1020 steel include:
- Carbon Content: 0.18% – 0.23%
- Manganese Content: 0.30% – 0.60%
- Tensile Strength: 440 MPa to 570 MPa
- Yield Strength: 290 MPa to 350 MPa
- Hardness: Brinell Hardness of 120-170
1020 steel is often used in applications such as shafts, gears, and other machinery parts due to its good balance of hardness, strength, and formability.
What is A36 Steel?
A36 steel, also known as ASTM A36 steel, is a low-carbon steel with a higher percentage of carbon than 1020 steel, typically around 0.26% carbon content. It is primarily known for its excellent weldability, machinability, and formability. The steel is frequently used for structural applications, such as in the construction of bridges, buildings, and other infrastructure.
Key properties of A36 steel include:
- Carbon Content: 0.26%
- Manganese Content: 0.60% – 0.90%
- Tensile Strength: 400 MPa to 550 MPa
- Yield Strength: 250 MPa (36,000 psi)
- Hardness: Brinell Hardness of 119-159
A36 steel is often used in structural beams, channels, plates, and other forms of structural components because of its ability to withstand stress and its ease of fabrication.
Key Differences Between 1020 Steel and A36
The comparison of 1020 steel vs A36 boils down to differences in chemical composition, mechanical properties, and intended applications. Here’s a table summarizing the primary differences between these two types of steel:
Property | 1020 Steel | A36 Steel |
---|---|---|
Carbon Content | 0.18% – 0.23% | 0.26% |
Tensile Strength | 440 MPa – 570 MPa | 400 MPa – 550 MPa |
Yield Strength | 290 MPa – 350 MPa | 250 MPa (36,000 psi) |
Manganese Content | 0.30% – 0.60% | 0.60% – 0.90% |
Hardness | Brinell 120-170 | Brinell 119-159 |
Weldability | Moderate | Excellent |
Applications | Machinery, automotive | Structural beams, frames |
Chemical Composition
- 1020 steel has slightly lower carbon content, which makes it more suitable for machining and forming into parts like shafts and gears.
- A36 steel, with its higher carbon content, offers improved structural integrity, making it ideal for large-scale construction projects.
Strength and Durability
- 1020 steel has a slightly higher tensile strength and yield strength than A36, which gives it an edge in applications requiring higher mechanical performance.
- A36 steel offers good strength for general structural purposes but isn’t as durable in high-stress environments compared to 1020 steel.
Mechanical Properties Comparison
Here’s a deeper look at the mechanical properties of 1020 steel vs A36 to help you understand how each material behaves under stress:
Mechanical Property | 1020 Steel | A36 Steel |
---|---|---|
Ultimate Tensile Strength | 440 – 570 MPa | 400 – 550 MPa |
Yield Strength | 290 – 350 MPa | 250 MPa |
Modulus of Elasticity | 200 GPa | 200 GPa |
Poisson’s Ratio | 0.29 | 0.26 |
Elongation at Break | 20% | 20% |
Hardness | 120-170 Brinell | 119-159 Brinell |
As we can see from the table, both steels have similar modulus of elasticity, which means their ability to deform elastically under stress is almost identical. However, 1020 steel tends to have slightly higher strength and hardness, making it more suitable for parts that will experience heavy wear and mechanical stress.
Applications of 1020 Steel and A36 Steel
Understanding the most common applications of 1020 steel vs A36 will help you determine which material is ideal for your project.
1020 Steel Applications
- Automotive Components: Gears, shafts, and other moving parts
- Machinery: Axles, spindles, and machine parts
- Tools and Equipment: Hand tools, dies, and molds
A36 Steel Applications
- Construction: Structural beams, columns, and steel plates
- Bridge Building: Supports and frames for bridges
- Infrastructure: Foundations, frames, and supports for buildings
The key takeaway is that 1020 steel is typically used for more precision-driven applications, while A36 steel is the go-to choice for large-scale structural applications.
Cost and Availability
Cost can be a deciding factor when choosing between 1020 steel vs A36. Generally, A36 steel is more cost-effective because it is more widely available and is used in mass production for structural purposes. 1020 steel, being used for more specific and high-performance applications, might cost slightly more depending on the grade and quantity needed.
Steel Type | Cost per Ton | Availability |
---|---|---|
1020 Steel | Higher ($650-$900) | Moderate |
A36 Steel | Lower ($500-$700) | Very High (readily available) |
Welding and Fabrication Considerations
One of the main advantages of A36 steel over 1020 steel is its exceptional weldability. A36 steel is designed for welding and can be welded using almost all welding methods, including MIG, TIG, and arc welding. This makes it ideal for large-scale construction projects where welding is a fundamental part of the fabrication process.
On the other hand, 1020 steel, while still weldable, may require more careful consideration during the welding process, especially with regard to preheating to avoid issues such as cracking.
FAQ
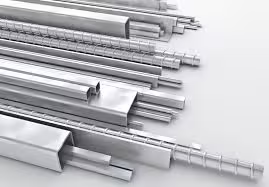
Q1: Can 1020 steel be used for structural applications like A36 steel?
While 1020 steel has good strength, A36 steel is typically preferred for large-scale structural applications due to its specific properties tailored for such uses.
Q2: Is 1020 steel better than A36 for welding?
A36 steel is generally easier to weld, making it a better choice for welding-intensive projects. 1020 steel requires more care when welding to prevent issues like cracking.
Q3: Which steel is better for high-precision parts?
1020 steel is more suited for precision machining, making it the better choice for parts such as gears, shafts, and tools.
Conclusion
The comparison between 1020 steel vs A36 highlights the importance of understanding material properties before selecting the best steel for your project. 1020 steel offers higher strength and is more suited for high-precision applications, while A36 steel excels in structural applications due to its excellent weldability and cost-effectiveness.
By considering factors such as tensile strength, welding capabilities, cost, and intended use, you can make an informed choice between 1020 steel vs A36. Always consult with a materials expert or engineer to ensure the best material selection for your specific needs.