
4140 Alloy: A Comprehensive Guide for Engineers
Introduction
4140 alloy steel is a high-strength, low-alloy steel known for its toughness and versatility in engineering applications. With a blend of chromium and molybdenum, alloy 4140 has become a go-to material in industries ranging from automotive to aerospace. This comprehensive guide aims to provide engineers with detailed insights into the properties, applications, heat treatment, and various considerations associated with 4140 alloy, ensuring informed decisions in material selection and application.
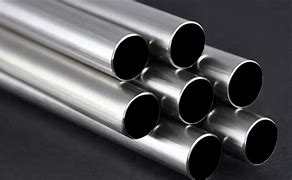
What is 4140 Alloy?
alloy 4140 steel is classified as a low alloy steel, featuring a carbon content ranging from 0.38% to 0.43%. The addition of chromium (0.8% to 1.1%) and molybdenum (0.15% to 0.25%) contributes to its high strength and toughness, making it suitable for demanding engineering tasks. The alloy is often used in its normalized, quenched, or tempered states, which further enhance its mechanical properties.
Chemical Composition of 4140 Alloy
The following table illustrates the typical chemical composition of 4140 alloy:
Element | Composition Range (%) |
---|---|
Carbon | 0.38 – 0.43 |
Manganese | 0.75 – 1.00 |
Phosphorus | 0.04 Max |
Sulfur | 0.04 Max |
Chromium | 0.8 – 1.1 |
Molybdenum | 0.15 – 0.25 |
This specific blend of elements is key to the alloy’s performance and suitability for various applications.
Mechanical Properties
The mechanical properties of alloy 4140 make it a preferred choice for many engineers. These properties include:
- Tensile Strength: Approximately 930 MPa
- Yield Strength: Around 655 MPa
- Hardness: Typically between 285 and 350 Brinell
- Elongation: 20-25%
Mechanical Properties Table
Property | Value |
---|---|
Yield Strength (MPa) | 655 |
Ultimate Tensile Strength (MPa) | 930 |
Elongation (%) | 20-25 |
Hardness (Brinell) | 285-350 |
These impressive mechanical properties are a significant reason for its extensive use in various engineering applications.
Heat Treatment of 4140 Alloy
Heat treatment is vital in enhancing the properties of alloy 4140. Different processes can optimize its hardness, strength, and ductility.
Quenching
Quenching involves heating the steel to around 850°C and rapidly cooling it in water or oil. This process hardens the steel but may increase brittleness.
Tempering
Tempering follows quenching and involves reheating the material to a lower temperature (around 400°C) to reduce brittleness while maintaining strength.
Annealing
Annealing is a slower cooling process that improves ductility and machinability, making it easier to work with during manufacturing.
Heat Treatment Process Summary
Treatment | Temperature (°C) | Purpose |
---|---|---|
Quenching | 850 | Hardens the alloy, increases brittleness |
Tempering | 400 | Reduces brittleness, maintains strength |
Annealing | 700 | Improves machinability and ductility |
Understanding these heat treatment processes allows engineers to tailor 4140 alloy to meet specific application requirements.
Applications of 4140 Alloy
The versatility of 4140 alloy makes it suitable for a wide range of applications. Below are some notable uses:
- Automotive Components: Crankshafts, gears, and axles benefit from the alloy’s high strength and durability.
- Aerospace Engineering: Components requiring high strength-to-weight ratios, such as landing gear and structural parts.
- Oil and Gas Industry: Drill bits and tubing where resistance to wear and high strength are critical.
- Heavy Machinery: Used in the manufacture of tools, shafts, and structural components.
- Construction: Employed in manufacturing beams, columns, and other structural elements.
Advantages of Using 4140 Alloy
Engineers choose 4140 alloy for several compelling reasons:
High Strength: Excellent tensile and yield strength makes it suitable for heavy-duty applications.
Versatility: Its range of mechanical properties allows it to be used in various industries.
Good Hardness: High wear resistance prolongs the life of components.
Heat Treatability: Can be heat treated to achieve desired characteristics based on application needs.
Challenges and Considerations
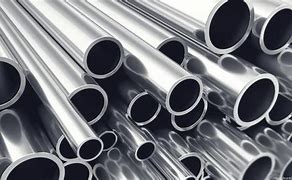
While 4140 alloy has numerous advantages, certain challenges must be addressed:
Weldability
Although 4140 alloy can be welded, it often requires pre-heating to avoid cracking due to its hardness.
Cost
As a low alloy steel, it can be more expensive than standard carbon steels, which may affect budget considerations.
Machinability
Machining 4140 requires specific tools and techniques due to its hardness. Tool wear can be significant if the wrong processes are used.
Corrosion Resistance
4140 alloy is not inherently corrosion-resistant, so protective coatings may be necessary depending on the application environment.
Comparison with Other Alloys
When comparing 4140 alloy to other common steels, it stands out due to its unique combination of strength and toughness. For example, while plain carbon steels may offer good machinability, they often lack the strength and wear resistance of 4140. Similarly, other high-alloy steels may exhibit superior corrosion resistance but may not match the mechanical properties of 4140 in structural applications.
Conclusion
4140 alloy steel is a highly versatile material that offers exceptional mechanical properties and durability, making it a popular choice among engineers. Its ability to withstand demanding conditions and be tailored through heat treatment further enhances its value across various industries. Understanding the properties, applications, and heat treatment processes of 4140 alloy is essential for engineers looking to make informed material choices for their projects.
FAQ
What is the main use of 4140 alloy?
alloy 4140 is primarily used in high-stress applications, such as automotive parts, aerospace components, and tools in the oil and gas industry.
Can 4140 alloy be welded?
Yes, while it can be welded, pre-heating is often necessary to prevent cracking.
What are the benefits of heat treating 4140 alloy?
Heat treating improves hardness, strength, and overall mechanical properties, making the alloy more suitable for various demanding applications.
Is 4140 alloy corrosion-resistant?
No, alloy 4140 is not inherently corrosion-resistant; protective coatings or treatments may be necessary for certain environments.
How does 4140 alloy compare to other alloys?
4140 offers a good balance of strength, toughness, and machinability, making it more versatile than some carbon steels while being less corrosion-resistant than higher alloy steels.
What are the machining considerations for 4140 alloy?
Effective machining requires specific tools and techniques to manage tool wear due to the alloy’s hardness.
Where can I find 4140 alloy materials?
alloy 4140 is widely available from steel suppliers and manufacturers, offered in forms such as bars, plates, and sheets.
By delving deeper into the aspects of 4140 alloy, engineers can better leverage its properties for optimal performance in various applications, ensuring reliability and effectiveness in their designs. Understanding its unique characteristics allows for the innovative application of this essential material in modern engineering.