
4140 Steel vs. Other Alloys: 6 Critical Differences
Table of Contents
Introduction
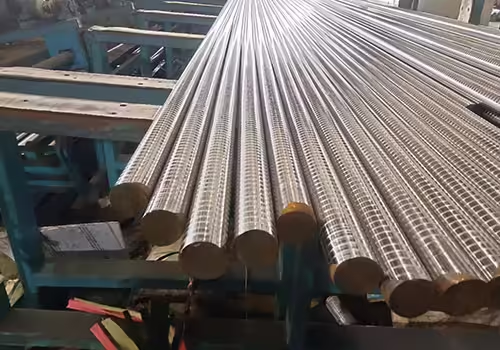
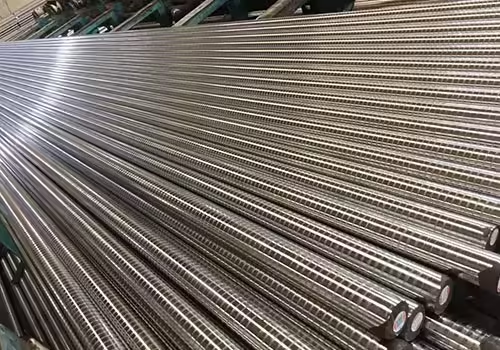
When selecting the right material for industrial projects, understanding the unique properties of different steels and alloys is crucial. Steel is one of the most commonly used materials in manufacturing, construction, and engineering, and choosing the right type can significantly impact the performance, cost, and longevity of products. Among the wide range of available steel alloys, 4140 steel stands out for its impressive combination of strength, durability, and versatility.
4140 steel is a low-alloy steel that contains chromium, molybdenum, and carbon, elements that contribute to its high strength, toughness, and wear resistance. However, to fully appreciate its benefits, it’s important to compare 4140 steel with other commonly used alloys such as 1045, 4130, 4340, and 1018. This article will break down the critical differences between 4140 steel and these alloys, helping you understand their distinct advantages, ideal applications, and when to choose one over the other.
What is 4140 Steel?
4140 steel is classified as a chromium-molybdenum alloy, which gives it a strong balance between hardenability and toughness. It contains 0.40% carbon, 0.80–1.10% chromium, and 0.15–0.25% molybdenum, contributing to its high tensile strength, resistance to wear and fatigue, and ability to perform under high temperatures.
One of the primary reasons 4140 steel is so widely used is its adaptability. It can be heat-treated to reach various hardness levels, and its composition can be altered to suit specific applications. Its strength and durability make it ideal for industries requiring materials that can handle heavy loads and harsh working environments.
Key Differences
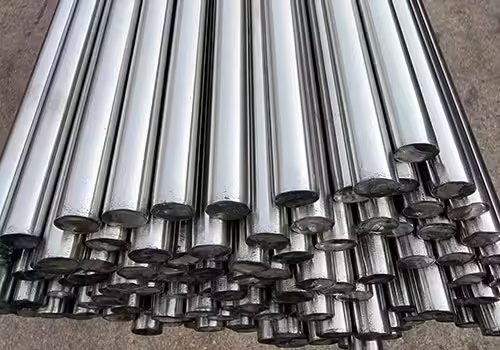
NO 1. Carbon Content and Hardness
Carbon content is one of the defining factors of steel alloys and influences their hardness, strength, and toughness.
4140 steel has a medium carbon content, ranging from 0.38% to 0.43%. This balanced carbon content provides a good mix of hardness and toughness, making it suitable for applications where both high strength and resistance to impact are necessary. When heat-treated, 4140 steel can achieve even higher hardness levels while maintaining its toughness.
In contrast, 1045 steel, another popular carbon steel, has a lower carbon content of 0.45%. This lower carbon content results in a softer, more ductile material compared to 4140 steel. While 1045 steel is easier to machine and weld, it is not as resistant to wear and impact as 4140, making it less suitable for high-stress applications.
For applications where extreme hardness is required, 4130 steel contains slightly less carbon (0.28–0.33%), and its strength comes primarily from its alloying elements like chromium and molybdenum. It is often used in aerospace applications due to its ability to withstand high stress and maintain a relatively low weight.
NO 2. Chromium and Molybdenum
Chromium and molybdenum are two essential alloying elements in 4140 steel. These elements contribute significantly to its strength, toughness, and resistance to wear and corrosion.
The chromium content in 4140 steel ranges from 0.80% to 1.10%. This enhances the alloy’s hardness and strength, as well as its resistance to oxidation and corrosion. Molybdenum, present in 0.15% to 0.25% concentrations, improves hardenability, making 4140 steel capable of achieving higher hardness levels when heat-treated. These elements also enhance the alloy’s resistance to fatigue, making it more durable under stress.
In comparison, alloys like 1018 steel do not contain significant amounts of chromium or molybdenum, meaning they are more susceptible to wear and corrosion. While 1018 steel is a cost-effective option for many applications, it is less durable and not suitable for use in harsh environments or high-stress conditions.
NO 3. Tensile Strength and Yield Strength Comparison
Tensile strength refers to a material’s ability to resist pulling forces, while yield strength refers to the amount of stress a material can endure before it starts to deform permanently.
4140 steel is known for its high tensile strength, which typically ranges from 660 MPa to 900 MPa, depending on the heat treatment process. This makes it ideal for heavy-duty applications where materials are subjected to intense stress, such as in tool shafts, gears, and automotive components. It also has a relatively high yield strength, which allows it to resist deformation under load.
In comparison, 4130 steel, which is also a chromium-molybdenum alloy, has a tensile strength of approximately 700 MPa, which is slightly higher than that of 4140 steel. However, 4130 is lighter and more suitable for aerospace applications, where weight is a critical factor.
Meanwhile, 1045 steel has a lower tensile strength, typically around 590 MPa, making it unsuitable for the same high-stress applications as 4140 steel. It is more appropriate for low-stress, general-purpose applications, such as mild shafts, bolts, and rods.
NO 4. Heat Treatment and Hardening
Heat treatment is an essential process for improving the hardness and wear resistance of steel. 4140 steel is highly heat-treatable and can undergo a variety of processes, including annealing, quenching, and tempering, to achieve the desired hardness and toughness.
When heat-treated, 4140 steel can achieve a Rockwell hardness of up to 50 HRC (Hardness Rockwell C), making it ideal for applications such as drilling, cutting, and machinery parts that require high strength and wear resistance. Its versatility in heat treatment allows for adjustments to meet specific project requirements.
Other alloys, such as 4340 steel, also benefit from heat treatment, but they require more specialized processes to achieve the same hardness as 4140. The increased complexity of heat treatment for alloys like 4340 can make them more expensive and time-consuming to process.
While 4130 steel can be heat-treated to achieve decent hardness, it does not achieve the same high hardness levels as 4140 steel, which limits its use in certain high-wear applications. Similarly, 1018 and 1045 steel alloys have limited hardening capabilities and are typically used in applications where lower hardness is acceptable.
NO 5. Wear Resistance and Durability
Wear resistance refers to a material’s ability to withstand abrasive wear caused by friction and mechanical interaction. One of the standout features of 4140 steel is its exceptional wear resistance, particularly when hardened.
4140 steel’s wear resistance makes it ideal for high-performance applications like heavy machinery parts, gears, and shafts that are exposed to constant friction and impact. Its toughness ensures that it can withstand repeated stress without cracking or deforming. When compared to 1018 steel, 4140 steel provides a far superior option for applications requiring wear resistance.
Alloys like 4340 steel, while offering excellent wear resistance, are often more expensive and not as readily available as 4140 steel. 4130 steel, on the other hand, offers good wear resistance but is often considered less durable than 4140 steel for high-stress applications.
Table: Key Properties of 4140 Steel vs. Other Alloys
Property | 4140 Steel | 1018 Steel | 1045 Steel | 4130 Steel | 4340 Steel |
---|---|---|---|---|---|
Carbon Content | Medium (0.38-0.43%) | Low (0.18-0.23%) | Medium (0.43-0.50%) | Medium (0.28-0.33%) | High (0.38-0.43%) |
Tensile Strength | High (~ 660 MPa) | Low (~ 440 MPa) | Medium (~ 590 MPa) | High (~ 700 MPa) | Very High (~ 750 MPa) |
Heat Treatment Ability | Excellent | Moderate | Good | Good | Excellent |
Wear Resistance | High | Low | Moderate | High | Very High |
Corrosion Resistance | Moderate | Low | Moderate | High | High |
Why Choose 4140 Steel Over Other Alloys?
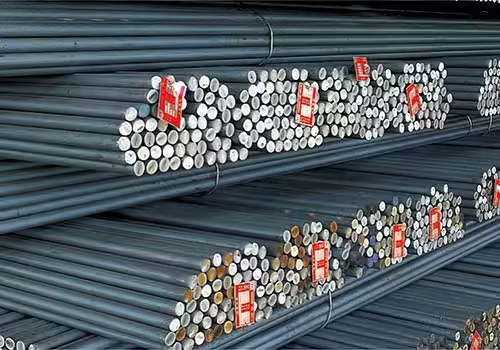
NO 1. Versatility in Applications
4140 steel is renowned for its versatility, making it a go-to material in various industries, including automotive, aerospace, manufacturing, and heavy machinery. This alloy is highly valued for its combination of strength, toughness, and adaptability to different heat treatments. Whether it is used in gears, shafts, tool parts, or structural components, its ability to be tailored for specific applications is one of its most significant advantages.
Compared to alloys like 1045 steel, which are often used in more general-purpose applications, or 1018 steel, which excels in ease of machining, 4140 steel truly shines in demanding environments. In particular, it is the material of choice in high-stress settings, where durability, toughness, and resistance to wear are essential. This makes it a crucial component in many industries, especially those dealing with heavy machinery or equipment subject to constant wear and tear.
NO 2. Superior Performance Under Stress
When it comes to performing under high stress, 4140 steel has an edge over many other alloys due to its impressive combination of tensile strength, wear resistance, and impact endurance. These properties make it the preferred choice for demanding applications such as heavy-duty machinery parts, automotive components, and high-performance tools.
While alloys like 4130 and 4340 are also excellent performers in certain applications—particularly aerospace, where lightweight materials are a key factor—4140 steel provides a solid, all-around solution for general heavy-duty use. Its ability to withstand immense mechanical stress and resist wear over time ensures that it delivers long-lasting performance without the need for the added costs associated with more specialized alloys. For many industrial applications, this combination of strength and affordability makes it an ideal choice for reliable performance.
Conclusion
Choosing the right material for your industrial application is essential to ensure optimal performance and longevity. 4140 steel offers a perfect balance of strength, toughness, and wear resistance, making it a popular choice for many industries. While other alloys like 4130, 1045, and 4340 offer unique benefits, 4140 steel remains a top contender for general-purpose applications requiring durability and resilience under stress.
When considering your options, remember that the choice of steel alloy will depend on factors such as the specific performance requirements, the level of wear resistance needed, and the cost-effectiveness for your project.
FAQ
What is the main advantage of 4140 steel over other alloys?
The primary benefit of 4140 steel is its exceptional balance of hardness, toughness, and resistance to wear, which makes it highly suitable for heavy-duty applications. Its ability to withstand high-stress environments without compromising its strength or durability gives it a distinct edge over many other alloys. In particular, its resistance to impact and fatigue makes it ideal for components subjected to intense mechanical stresses.
Can 4140 steel be used in aerospace?
While 4140 steel is versatile and can be used in the aerospace industry, it is more commonly utilized for parts that require a high level of strength and wear resistance, such as landing gear components, structural parts, and other heavy-duty components. However, for weight-sensitive applications like aircraft bodies or wings, lighter alloys may be preferred. That being said, it still plays a critical role in ensuring the safety and reliability of aerospace systems, thanks to its robust mechanical properties.
How does 4140 steel compare to 4130 steel?
Both 4140 and 4130 steels belong to the same chromium-molybdenum family, but they differ in a few key areas. The most notable difference is that the former tends to offer a higher tensile strength, superior toughness, and better resistance to wear. This makes it more suitable for applications requiring heavy-duty performance under demanding conditions. On the other hand, 4130 steel, while still a high-strength material, is often preferred in industries where weight-saving is a critical factor, such as aerospace. Thus, the choice between these two alloys largely depends on the specific requirements of the project, including stress tolerance and weight considerations.
Is 4140 steel cost-effective?
When considering the long-term durability and performance of the material, 4140 steel is often seen as a highly cost-effective option. While the initial cost may be higher than simpler steels like 1018 or 1045, its superior mechanical properties—such as its ability to resist wear, its toughness, and its longevity in harsh environments—make it a cost-efficient choice over time. Additionally, due to its versatility and ease of heat treatment, it can be used in a wide range of applications, making it a solid investment for industries that require high-strength materials for demanding conditions.
What industries use 4140 steel?
4140 steel is widely used across numerous industries due to its high performance and adaptability. Key sectors that rely on this alloy include the automotive industry (for engine parts, shafts, and gears), aerospace (for landing gear, structural components, and more), manufacturing (for tools, dies, and heavy machinery), and the construction industry (for structural elements and equipment). Its ability to perform under stress makes it essential in applications that require high strength, fatigue resistance, and toughness. Additionally, 4140 steel is also used in the oil and gas, mining, and defense sectors, where reliability and durability are critical.