
42CrMo4 Hardness: A Guide for Industrial Use
Table of Contents
Introduction
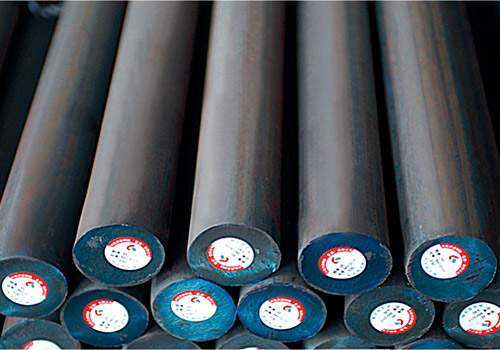
42CrMo4 is a low-alloy steel known for its high strength, toughness, and wear resistance. Its exceptional properties make it a popular choice in various industries, including automotive, aerospace, and heavy machinery. Among its many attributes, hardness plays a critical role in determining its suitability for specific applications.
This guide explores the significance of 42CrMo4 hardness, its measurement, applications, and how its properties can be optimized to meet industrial needs. By the end of this article, you will have a comprehensive understanding of why 42CrMo4 is a preferred material for demanding environments.
Understanding 42CrMo4 Hardness
What is 42CrMo4?
42CrMo4 is a chromium-molybdenum steel with a balanced chemical composition that offers excellent mechanical properties. It is often used in applications requiring high strength and fatigue resistance.
The Importance of Hardness
Hardness is a material’s ability to resist deformation, wear, and abrasion. For 42CrMo4, hardness directly impacts its performance in high-stress and high-wear environments. Proper heat treatment and tempering can optimize its hardness to suit different industrial requirements.
Common Hardness Scales for 42CrMo4
The hardness of 42CrMo4 is typically measured using standardized scales such as Rockwell (HRC), Brinell (HB), or Vickers (HV). These measurements provide insights into the material’s resistance to surface deformation and its durability under stress.
Heat Treatment and Hardness of 42CrMo4
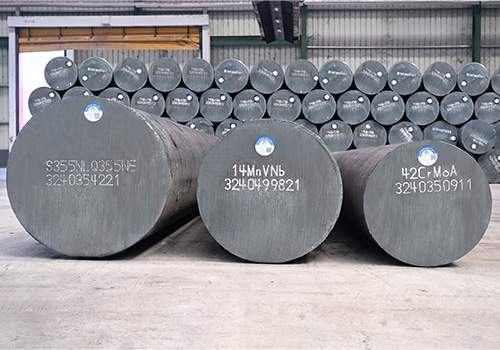
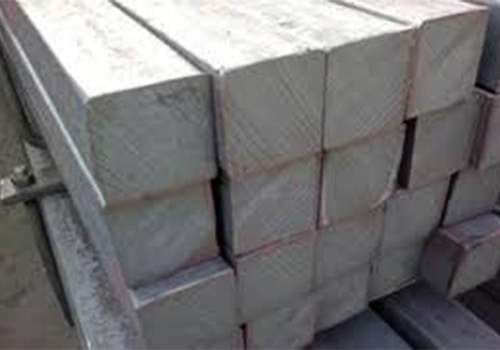
Heat Treatment Processes
- Annealing
- Reduces hardness and improves machinability.
- Refines the grain structure for enhanced toughness.
- Quenching
- Increases hardness by rapidly cooling the material after heating.
- Provides a hardened structure suitable for wear-resistant applications.
- Tempering
- Balances hardness and toughness.
- Reduces brittleness introduced by quenching.
Hardness Achieved Through Heat Treatment
The final hardness of 42CrMo4 depends on the heat treatment parameters, including temperature, cooling rate, and tempering conditions.
Factors Influencing Hardness
- Chemical Composition
Chromium and molybdenum enhance hardenability and resistance to wear. - Cooling Medium
Oil, water, or air cooling can significantly affect hardness. - Tempering Temperature
Higher tempering temperatures reduce hardness but increase ductility.
Applications of 42CrMo4 Based on Hardness
42CrMo4’s versatility stems from its ability to achieve varying hardness levels, making it suitable for diverse industrial applications.
Automotive Industry
- Crankshafts: High hardness ensures wear resistance.
- Connecting Rods: Combines hardness with fatigue resistance.
Aerospace Industry
- Landing Gear Components: Requires high strength and durability.
- Engine Parts: Optimized hardness enhances performance under extreme conditions.
Machinery and Tooling
- Gears: High surface hardness minimizes wear.
- Mold Components: Hardness contributes to prolonged service life.
Oil and Gas Industry
- Drill Collars: High hardness resists abrasive environments.
- Valve Components: Withstands high-pressure operations.
Comparative Hardness of 42CrMo4
Treatment Process | Typical Hardness (HRC) | Application Examples |
---|---|---|
Annealed | 18-22 | Machining and forming applications |
Quenched and Tempered | 28-34 | Structural components |
Quenched and Tempered at High Temperatures | 38-44 | Tools and machinery parts requiring durability |
Surface Hardened | 55-60 | Gears and high-wear surfaces |
Optimizing 42CrMo4 Hardness for Specific Uses
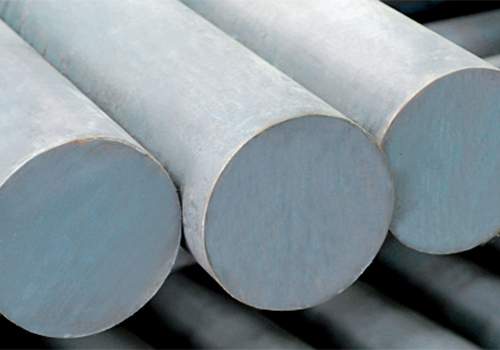
Selecting the Right Heat Treatment
Depending on the intended application, the heat treatment process can be tailored to achieve the desired balance between hardness and toughness.
Surface Treatments
Processes like carburizing or nitriding can increase surface hardness while maintaining core ductility, ideal for wear-intensive applications.
Testing and Quality Control
Regular hardness testing ensures consistency and reliability in performance. Advanced techniques such as microhardness testing can assess localized hardness variations.
Conclusion
42CrMo4’s hardness is a critical property that defines its utility across industries. With proper heat treatment, this versatile steel can meet the demands of applications ranging from automotive to aerospace. Understanding the relationship between hardness, heat treatment, and performance enables industries to leverage 42CrMo4 to its full potential.
Whether you are selecting materials for heavy-duty tools or precision components, the tailored hardness of 42CrMo4 offers unmatched reliability and performance.
FAQ
What is the typical hardness range of 42CrMo4?
The hardness of 42CrMo4 varies based on heat treatment, typically ranging from 18 HRC (annealed) to 60 HRC (surface-hardened).
How is the hardness of 42CrMo4 measured?
Common methods include the Rockwell (HRC), Brinell (HB), and Vickers (HV) hardness tests.
Why is heat treatment important for 42CrMo4?
Heat treatment optimizes the material’s hardness, toughness, and wear resistance, making it suitable for specific industrial applications.
Can 42CrMo4 be welded?
Yes, but due to its high hardenability, preheating and post-weld heat treatment are recommended to prevent cracking.
What industries commonly use 42CrMo4?
Industries such as automotive, aerospace, machinery, and oil and gas extensively use 42CrMo4 for its strength and hardness.
What is the role of chromium and molybdenum in 42CrMo4?
Chromium improves hardenability and corrosion resistance, while molybdenum enhances toughness and resistance to high temperatures.
How does tempering affect the hardness of 42CrMo4?
Tempering reduces brittleness introduced during quenching and adjusts hardness based on the tempering temperature.
Are there alternatives to 42CrMo4 with similar hardness?
Yes, materials like 4140 and 4340 steels offer comparable properties, though specific applications may favor one over the other.
Is surface hardening recommended for 42CrMo4?
Yes, processes like carburizing or nitriding can enhance surface wear resistance while maintaining core toughness.
Can 42CrMo4 be used in high-temperature applications?
Yes, its composition and heat treatment make it suitable for high-stress, high-temperature environments.