
7 Things You Didn’t Know About Alloy Steel’s Durability
Table of Contents
Introduction
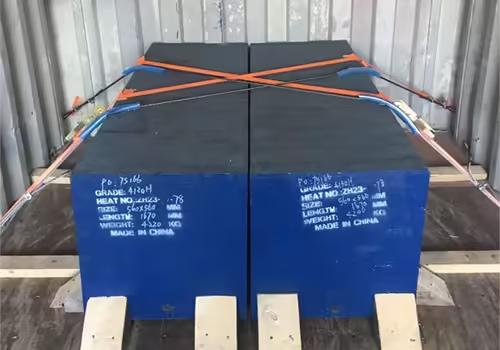
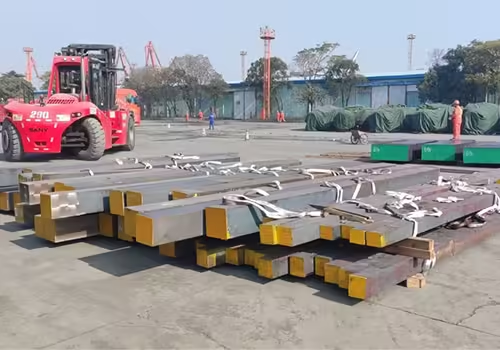
When it comes to materials that have transformed modern engineering, few can match the versatility and resilience of alloy steel. Renowned for its strength and adaptability, this material has become a cornerstone in industries ranging from construction to aerospace. However, beyond its well-known attributes, there are several fascinating aspects of its durability that often go unnoticed. In this blog, we’ll explore seven intriguing facts about the endurance of this remarkable material, shedding light on its unique composition, resistance to harsh conditions, and its role in advancing technology. Whether you’re an engineer, a manufacturer, or simply curious, these insights will deepen your appreciation for this indispensable material.
What Makes Alloy Steel So Durable?
The Role of Alloying Elements
The exceptional durability of this material stems from its unique blend of elements. Unlike traditional carbon steel, it incorporates additional components such as manganese, nickel, chromium, and molybdenum. These elements work together to enhance its mechanical properties, including hardness, toughness, and resistance to wear. For example, chromium boosts its ability to resist corrosion, while molybdenum ensures it maintains strength even under extreme heat. This combination of elements allows it to perform reliably in diverse environments, from the depths of the ocean to the high temperatures of industrial machinery.
Microstructure and Heat Treatment
Another key factor in its durability lies in its microstructure, which can be precisely controlled through heat treatment processes. Techniques such as quenching and tempering modify the internal structure of the material, optimizing its strength and toughness. This ability to tailor its properties makes it an ideal choice for applications that demand materials capable of withstanding intense stress and wear. For instance, in the automotive industry, components like gears and axles benefit from this enhanced durability, ensuring they perform reliably over long periods.
Resistance to Fatigue and Fracture
In addition to its strength, this material is highly resistant to fatigue and fracture, making it suitable for applications involving repetitive stress. This property is particularly valuable in industries like aviation, where components must endure constant pressure without failing. By incorporating elements like vanadium and nickel, the material’s ability to resist cracking under cyclic loads is significantly improved, ensuring longevity and safety in critical applications.
Adaptability to Various Environments
One of the most impressive aspects of this material is its adaptability. Whether exposed to extreme temperatures, corrosive substances, or heavy mechanical loads, it consistently delivers reliable performance. This adaptability is achieved through careful selection of alloying elements and precise manufacturing processes, making it a go-to solution for industries that operate in challenging conditions.
Cost-Effectiveness in the Long Run
While the initial cost of this material may be higher than that of traditional carbon steel, its long-term benefits often justify the investment. Its durability reduces the need for frequent replacements and repairs, lowering maintenance costs over time. This cost-effectiveness, combined with its superior performance, makes it a smart choice for industries looking to maximize efficiency and minimize downtime.
Alloy Steel’s Resistance to Corrosion
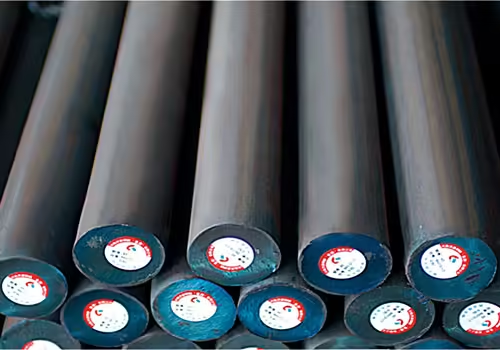
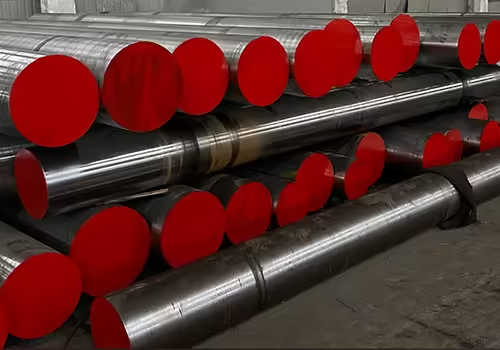
Chromium’s Protective Shield
One of the standout features of alloy steel is its resistance to corrosion, particularly in grades that contain chromium. When exposed to oxygen, chromium forms a thin, invisible layer of chromium oxide on the steel’s surface. This layer acts as a protective shield, preventing further oxidation and rusting. This property makes alloy steel ideal for applications in harsh environments, such as marine or chemical industries.
Comparing Corrosion Resistance
To better understand alloy steel’s corrosion resistance, let’s compare it to other common materials in the table below:
Material | Corrosion Resistance | Common Applications |
---|---|---|
Alloy Steel | High | Marine, chemical, oil & gas |
Carbon Steel | Low | Construction, machinery |
Stainless Steel | Very High | Food processing, medical |
Aluminum | Moderate | Aerospace, automotive |
As shown, alloy steel strikes a balance between durability and corrosion resistance, making it a versatile choice for many industries.
Performance in High-Temperature Applications
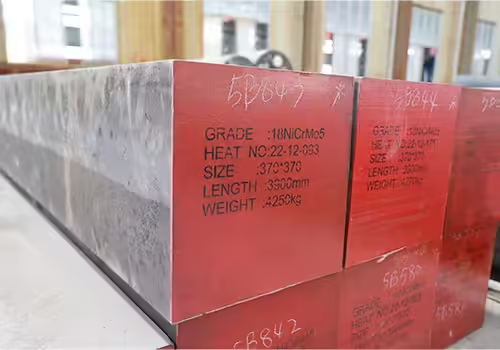
Retaining Strength Under Heat
One of the standout features of this material is its ability to retain strength even when exposed to elevated temperatures. Specific grades, particularly those infused with elements like molybdenum and vanadium, are engineered to excel in high-temperature environments. These grades are indispensable in industries such as power generation, where components must withstand extreme heat and pressure without compromising performance. For example, in gas turbines, the blades and rotors are often made from these specialized grades to ensure they can operate efficiently under intense thermal stress.
Thermal Expansion and Stability
Another critical factor in high-temperature applications is the material’s low thermal expansion. This means it does not undergo significant dimensional changes when exposed to heat, a property that is essential for maintaining precision and reliability. In applications like jet engines or industrial furnaces, where components must fit and function perfectly under fluctuating temperatures, this stability ensures consistent performance and reduces the risk of failure.
Resistance to Thermal Fatigue
In addition to retaining strength and stability, this material is highly resistant to thermal fatigue, which occurs when repeated heating and cooling cycles cause stress and eventual cracking. This resistance is particularly valuable in applications like thermal power plants, where equipment undergoes constant temperature variations. By withstanding these cycles without degrading, the material helps extend the lifespan of critical components, reducing maintenance costs and downtime.
Applications in Aerospace and Energy
The aerospace and energy sectors heavily rely on this material for high-temperature applications. In aerospace, components like turbine discs and exhaust systems are subjected to extreme heat during operation. Similarly, in the energy sector, parts like boiler tubes and heat exchangers must endure prolonged exposure to high temperatures. The material’s ability to perform under these conditions makes it a cornerstone of innovation in these industries.
Wear Resistance and Longevity
Hardness and Toughness
The exceptional wear resistance of this material is a direct result of its hardness and toughness, which are enhanced through careful alloying and heat treatment processes. These properties make it highly resistant to abrasion, erosion, and surface degradation, even when subjected to heavy loads. Industries such as mining, construction, and manufacturing depend on this material for equipment that must endure constant wear and tear without failing.
Case Study: Mining Equipment
In the mining industry, components like drill bits, crushers, and conveyor systems are exposed to some of the harshest conditions imaginable. Abrasive materials, heavy impacts, and continuous use can quickly degrade lesser materials. However, this material’s durability ensures that such equipment remains operational for extended periods, minimizing downtime and maintenance costs. For instance, drill bits made from this material can penetrate tough rock formations without losing their edge, while crushers can process large volumes of material without succumbing to wear.
Applications in Heavy Machinery
Beyond mining, this material is also widely used in heavy machinery, such as bulldozers, excavators, and loaders. These machines operate in demanding environments where wear and tear are inevitable. By using components made from this durable material, manufacturers can ensure their equipment remains reliable and efficient, even under the most challenging conditions.
Contribution to Cost Efficiency
The longevity of this material translates into significant cost savings for industries that rely on heavy equipment. By reducing the frequency of replacements and repairs, companies can lower their operational costs and improve productivity. This cost efficiency, combined with the material’s superior performance, makes it an invaluable asset in industries where durability is paramount.
Innovations in Wear-Resistant Coatings
Recent advancements in material science have led to the development of specialized coatings that further enhance wear resistance. These coatings, often applied to components made from this material, provide an additional layer of protection against abrasion and erosion. This innovation is particularly beneficial in industries like oil and gas, where equipment is exposed to abrasive particles and corrosive substances.
Alloy Steel’s Impact on Sustainability
Recyclability and Environmental Benefits
Alloy steel is not only durable but also environmentally friendly. It is 100% recyclable, meaning it can be reused without losing its properties. This reduces the need for raw materials and minimizes waste, contributing to a more sustainable manufacturing process. Industries are increasingly adopting alloy steel to meet environmental regulations and reduce their carbon footprint.
Energy Efficiency in Production
The production of alloy steel is also energy-efficient compared to other materials. Advanced manufacturing techniques and the use of recycled steel significantly lower energy consumption, making alloy steel a greener choice for various applications.
Common Myths About Alloy Steel
Myth: Alloy Steel is Always Expensive
While alloy steel can be more expensive than plain carbon steel, its long-term benefits often outweigh the initial cost. Its durability and low maintenance requirements make it a cost-effective solution for many applications.
Myth: Alloy Steel is Difficult to Work With
Another misconception is that alloy steel is challenging to machine or weld. In reality, modern techniques and tools have made it easier to work with alloy steel, allowing for precise and efficient manufacturing processes.
Conclusion
Alloy steel’s durability is a result of its unique composition, heat treatment processes, and resistance to extreme conditions. Its ability to withstand corrosion, high temperatures, and wear makes it an invaluable material across numerous industries. Additionally, its recyclability and energy-efficient production contribute to a more sustainable future. By understanding these lesser-known aspects of alloy steel’s durability, we can better appreciate its role in modern engineering and manufacturing. Whether you’re designing machinery, constructing infrastructure, or developing innovative technologies, alloy steel offers the strength and reliability needed to succeed.
FAQ
What is alloy steel?
Alloy steel is a type of steel that contains additional elements like chromium, nickel, and molybdenum to enhance its mechanical properties.
How does alloy steel compare to stainless steel?
While both materials are durable, alloy steel offers a balance of strength and corrosion resistance, whereas stainless steel is primarily known for its exceptional corrosion resistance.
Can alloy steel be used in extreme temperatures?
Yes, certain grades of alloy steel are designed to perform well in high-temperature environments, making them suitable for applications like power generation and aerospace.
Is alloy steel environmentally friendly?
Absolutely. Alloy steel is 100% recyclable and its production process is energy-efficient, making it a sustainable choice for various industries.