
Understanding 4140 Composition and Its Key Properties
Table of Contents
Introduction
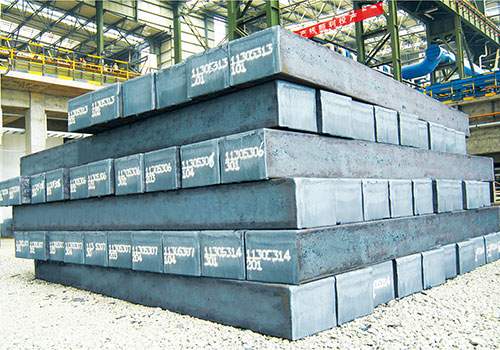
Steel alloys form the backbone of modern industries, providing materials with superior mechanical properties that are essential for a range of demanding applications. Among these alloys, 4140 steel stands out due to its excellent balance of strength, durability, and toughness. This steel is widely used in industries such as automotive, aerospace, oil and gas, and tool manufacturing. In this blog, we will examine the composition of 4140 steel, its key properties, and its uses, while highlighting why it is a go-to material for various industrial sectors.
4140 steel is a chromium-molybdenum alloy that exhibits high tensile strength, resistance to wear and fatigue, and the ability to withstand extreme temperatures. Understanding the composition and properties of this steel will provide valuable insights into how it performs in different applications and why it is so well-suited for specific industrial needs.
What Is 4140 Composition?
4140 steel is primarily composed of carbon, chromium, molybdenum, and other alloying elements, which combine to give the material its outstanding mechanical properties. The precise composition of these elements is what allows 4140 steel to provide an optimal combination of strength, toughness, and resistance to wear and impact.
Breakdown of 4140 Steel Composition
- Carbon (C): 0.38% – 0.43%
Carbon is the fundamental alloying element in steel that increases hardness and strength. However, too much carbon can make the steel brittle. The moderate carbon content of 4140 steel ensures that it is both strong and ductile, making it ideal for high-stress applications. - Chromium (Cr): 0.80% – 1.10%
Chromium adds corrosion resistance to steel, which helps prevent rust and oxidation when the steel is exposed to moisture or harsh chemicals. It also increases the hardness of the steel, which makes it more suitable for heat treatment. - Molybdenum (Mo): 0.15% – 0.25%
Molybdenum improves 4140 steel’s resistance to high temperatures and wear. It also enhances the steel’s toughness and helps maintain its strength, even at elevated temperatures. Molybdenum is especially valuable for tools and parts that experience high levels of friction. - Manganese (Mn): 0.60% – 0.90%
Manganese helps improve the hardness and tensile strength of 4140 steel. It also serves as a deoxidizing agent, removing oxygen during the steelmaking process and improving the material’s overall ductility. - Silicon (Si): 0.20% – 0.35%
Silicon contributes to the steel’s overall strength and plays a vital role in the deoxidization of molten steel. It also helps improve the material’s hardness and resistance to corrosion. - Sulfur (S) and Phosphorus (P): Traces (less than 0.04%)
These elements are typically present in minimal amounts as they can reduce the ductility and toughness of the steel. Lower sulfur and phosphorus content is crucial to maintaining the steel’s integrity.
With this precise combination of elements, 4140 steel is capable of withstanding high mechanical stresses while maintaining excellent toughness and wear resistance.
Key Properties of 4140 Steel
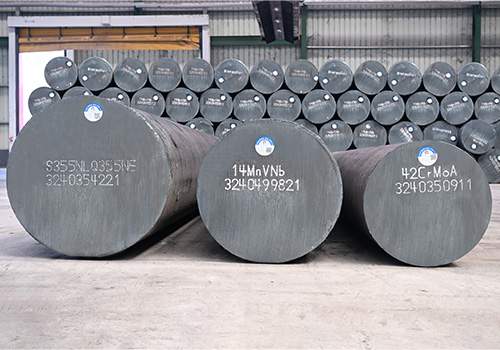
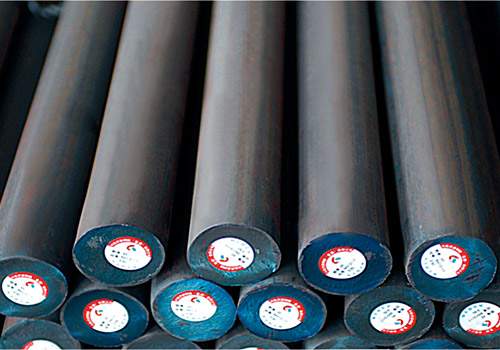
4140 steel is known for its impressive range of mechanical properties, which include high tensile strength, excellent wear resistance, and impressive fatigue resistance. These properties make it an ideal material for applications in industries where durability and performance are critical.
High Strength and Toughness
One of the most important characteristics of 4140 steel is its high tensile strength, which makes it suitable for applications where materials are subjected to heavy loads. The combination of strength and toughness in 4140 steel allows it to resist breaking or cracking under stress. This is particularly beneficial for components used in high-impact environments, such as automotive and aerospace parts.
Good Wear and Corrosion Resistance
Chromium and molybdenum enhance the steel’s resistance to both wear and corrosion. 4140 steel maintains its integrity even in harsh environments, where parts are exposed to abrasion, chemical corrosion, or high-temperature stress. This property makes it a preferred choice for tools, shafts, and gears that require long-lasting durability.
Heat Treatability
4140 steel is highly responsive to heat treatment processes. Heat treatments such as quenching and tempering can increase the steel’s hardness and tensile strength. This allows manufacturers to tailor the properties of the material for specific needs, such as achieving higher hardness for cutting tools or more ductility for structural components.
Ductility and Formability
Despite its high strength, 4140 steel retains a good level of ductility, meaning it can be shaped and formed into a variety of parts. This makes it versatile for use in industries that require both strong and easily formable materials. Its weldability is also an important aspect, though post-weld heat treatment is often required to restore its mechanical properties after welding.
Fatigue and Impact Resistance
The alloy composition of 4140 steel provides outstanding resistance to fatigue and impact. This is crucial for parts that will be subjected to repetitive stresses, such as crankshafts, gears, and drive shafts. The steel’s ability to resist cracking and failure in these situations makes it an excellent material for automotive and machinery components.
Table: Key Properties of 4140 Steel
Property | Value |
---|---|
Carbon Content (C) | 0.38% – 0.43% |
Chromium Content (Cr) | 0.80% – 1.10% |
Molybdenum Content (Mo) | 0.15% – 0.25% |
Manganese Content (Mn) | 0.60% – 0.90% |
Silicon Content (Si) | 0.20% – 0.35% |
Tensile Strength | 655 MPa to 850 MPa |
Yield Strength | 415 MPa to 690 MPa |
Hardness (Brinell) | 200 – 250 HB |
Elongation | 15% – 25% |
Impact Toughness | Excellent resistance to fracture |
Corrosion Resistance | Good (due to Chromium and Molybdenum) |
Heat Treatability | Good (Hardenable through quenching) |
Applications of 4140 Steel
Due to its excellent mechanical properties, 4140 steel is used in various industries. Some of the most common applications include:
Automotive Industry
4140 steel is often used for the production of components like axles, crankshafts, gears, and suspension parts. The high strength, toughness, and wear resistance of 4140 make it suitable for components subjected to heavy loads and continuous stress, as is the case in vehicles.
Aerospace Industry
In aerospace, 4140 steel is used in the manufacture of turbine shafts, landing gear, and structural supports. The material’s high tensile strength and resistance to high temperatures make it ideal for parts that experience extreme conditions.
Oil and Gas Industry
In the oil and gas sector, 4140 steel is used for drill pipes, valves, and other critical components. The steel’s corrosion resistance and ability to withstand high pressure and impact make it a reliable material for such challenging environments.
Tool Manufacturing
4140 steel is commonly used in the production of tooling and equipment such as dies, molds, and cutting tools. The steel’s hardness and wear resistance make it a strong candidate for applications requiring precision and durability.
Construction and Infrastructure
The durability and strength of 4140 steel make it a valuable material for structural components in construction and infrastructure projects. It is used for beams, bridges, and other load-bearing elements, ensuring that these structures maintain their integrity over time.
Factors Affecting 4140 Steel’s Performance
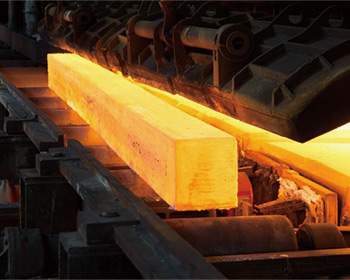
Several factors influence the performance of 4140 steel. Understanding these can help ensure that the material performs optimally for its intended application.
Heat Treatment Process
The heat treatment process significantly affects the mechanical properties of 4140 steel. Proper quenching and tempering can enhance the hardness and tensile strength, making the steel ideal for use in high-stress applications. The method of heat treatment and the temperature at which it occurs directly influence the final properties of the steel.
Manufacturing Method
The method used to manufacture 4140 steel—whether through forging, casting, or rolling—can affect its properties. Forged 4140 steel tends to have superior mechanical properties compared to cast or rolled versions due to the alignment of grain structures during the forging process.
Environmental Conditions
Exposing 4140 steel to extreme environmental conditions such as high heat or corrosive substances can affect its performance. However, the alloy’s inherent resistance to corrosion and heat is a significant advantage in such environments. Additional protective coatings or heat treatments can further enhance its resistance to corrosion and wear.
Conclusion
4140 steel offers a unique combination of strength, toughness, and wear resistance, making it an essential material for industries that require high-performance components. Its precise composition and response to heat treatment processes allow it to be tailored to meet specific application requirements. Whether you’re working in automotive, aerospace, oil and gas, or construction, 4140 steel is a reliable material that ensures longevity and safety in demanding environments.
Understanding 4140 steel’s composition and properties can guide engineers and manufacturers in making informed decisions about material selection. The ability to customize its mechanical properties through heat treatment makes it an adaptable solution for a wide range of applications.
FAQ
What makes 4140 steel so popular in industrial applications?
4140 steel is favored for its combination of high strength, toughness, resistance to wear, and heat treatability. These properties make it ideal for use in demanding industries such as automotive, aerospace, and manufacturing.
How does the heat treatment of 4140 steel affect its properties?
Heat treatment processes like quenching and tempering increase the hardness, tensile strength, and impact resistance of 4140 steel. This enables manufacturers to customize the material’s properties based on the specific requirements of their applications.
Can 4140 steel be welded?
Yes, 4140 steel can be welded, but special care must be taken during the welding process. Proper pre- and post-weld heat treatment is required to ensure that the steel maintains its strength and toughness after welding.
What industries commonly use 4140 steel?
4140 steel is used in industries such as automotive, aerospace, oil and gas, tool manufacturing, and construction. It is commonly found in components like gears, shafts, drill pipes, and structural supports.
How does the addition of molybdenum and chromium benefit 4140 steel?
Molybdenum improves 4140 steel’s resistance to heat and wear, while chromium enhances its corrosion resistance. These elements work together to give 4140 steel the durability and strength needed for heavy-duty applications.