
How 1020 Steel Hardness Affects Performance
Table of Contents
Introduction
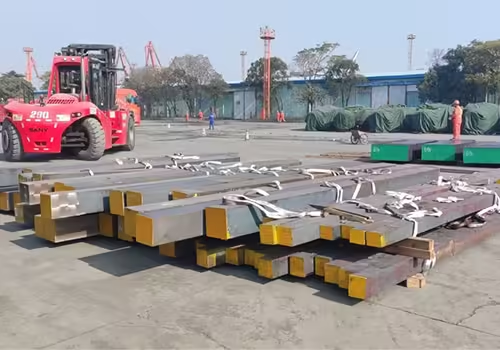
1020 steel is a low-carbon steel alloy known for its good balance of strength, toughness, and ease of machinability. One of the critical factors that influence the performance of 1020 steel is its hardness. Hardness in steel refers to its resistance to indentation, wear, and deformation under stress. Understanding how 1020 steel hardness affects its performance is crucial for industries that rely on steel for structural and manufacturing purposes.
This article will delve into the various aspects of 1020 steel hardness, how it impacts the material’s performance in different applications, and why it’s essential to consider this property when choosing the right material for a job.
Henan Jiyuan Iron and Steel (Group) Co., Ltd. was founded in 1958. It has rich experience in production and research and development. It provides you with one-stop steel services and welcomes consultations from customers around the world.
What is 1020 Steel Hardness?
1020 steel is classified as a medium-carbon steel with a carbon content of approximately 0.20%. This level of carbon makes it malleable and easily welded, which is why it’s commonly used in applications such as shafts, gears, and automotive parts. However, the hardness of 1020 steel can vary based on heat treatment processes, alloying elements, and the environment in which it is used.
Hardness is measured using various scales, such as the Rockwell, Brinell, and Vickers scales, each offering a different method of assessing the resistance of the steel to indentation. The typical hardness range for 1020 steel lies between 120 and 190 HB (Brinell Hardness), depending on the heat treatment applied.
How Does 1020 Steel Hardness Affect Performance?
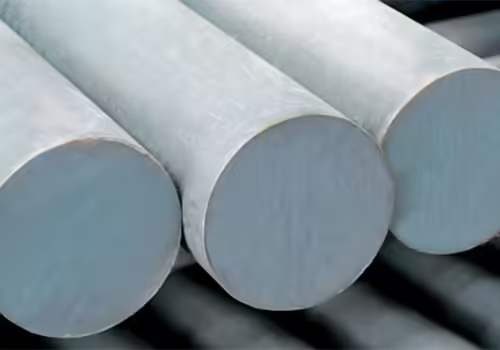
The hardness of 1020 steel significantly influences its mechanical properties and suitability for various applications. Below are the key ways that hardness affects its performance:
Strength and Durability
Harder steel tends to have higher tensile strength, meaning it can withstand greater forces before breaking. In applications that involve high stress, such as heavy-duty machinery or construction equipment, the hardness of 1020 steel plays a crucial role in determining its durability. Harder 1020 steel will be more resistant to wear and tear, making it ideal for long-term use in such environments.
Wear Resistance
Hardness directly impacts the wear resistance of 1020 steel. Materials that are harder generally show better resistance to abrasive wear, which is essential in environments where steel components are exposed to friction and abrasion, such as automotive components or industrial machinery. Hardening processes can enhance this property by increasing the steel’s surface hardness.
Machinability
While harder steel provides better resistance to wear, it can be more challenging to machine. The increased hardness of 1020 steel might result in higher tool wear and the need for more specialized machining equipment. In contrast, softer 1020 steel is easier to machine but may sacrifice some strength and durability. Finding the right balance between hardness and machinability is essential for producing quality components.
Toughness and Brittleness
As the hardness of 1020 steel increases, its toughness tends to decrease. This is because harder steels are often more brittle, making them prone to cracking under impact or stress. Therefore, while harder 1020 steel offers superior wear resistance, it may not be as suitable for applications that require high impact resistance or flexibility. On the other hand, slightly softer 1020 steel may be more suitable for shock-loading conditions.
Corrosion Resistance
Although hardness does not directly affect corrosion resistance, the processes involved in hardening 1020 steel—such as carburizing—can affect the material’s ability to resist corrosion. In some cases, a hardened steel surface may develop a protective oxide layer that improves corrosion resistance. However, this depends on the heat treatment method used and the environment in which the steel is exposed.
Table: The Impact of 1020 Steel Hardness on Various Properties
Hardness Level (HB) | Strength (MPa) | Durability (Months) | Machinability | Wear Resistance | Toughness (J) |
---|---|---|---|---|---|
120-140 | 370 | 12-15 | Easy | Low | 55 |
140-160 | 410 | 15-20 | Moderate | Moderate | 50 |
160-180 | 450 | 20-25 | Moderate | High | 45 |
180-190 | 480 | 25-30 | Difficult | Very High | 40 |
Heat Treatment Methods to Enhance 1020 Steel Hardness
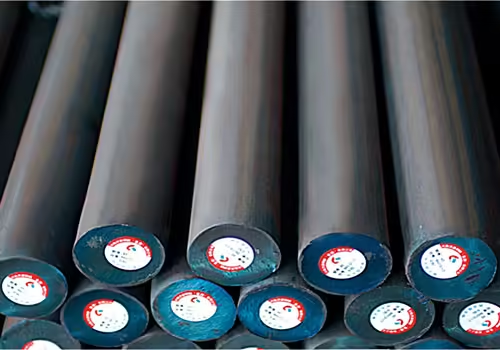
There are several methods used to increase the hardness of 1020 steel, each offering different benefits for performance. Below are the common heat treatment processes used to enhance 1020 steel hardness:
Carburizing
Carburizing involves adding carbon to the surface of the steel, which increases its hardness without affecting the entire material. This process results in a hard outer layer, which enhances wear resistance while retaining the toughness of the core. This is commonly used for parts that need to endure high friction but must also retain strength under heavy loads.
Quenching and Tempering
Quenching is a process where the steel is heated to a high temperature and then rapidly cooled, typically in oil or water. This process hardens the steel but can make it brittle. Tempering is done afterward by reheating the steel to a lower temperature and slowly cooling it to relieve internal stresses, improving toughness without sacrificing too much hardness. This combination of quenching and tempering allows for an optimized balance of hardness and toughness.
Annealing
Annealing is the opposite of hardening. It involves heating the steel and then cooling it slowly, which reduces its hardness but increases its ductility and machinability. This is ideal for applications where ease of machining is a priority, although the material may be less durable.
Applications of 1020 Steel in Different Hardness Ranges
The hardness of 1020 steel influences its suitability for various applications. Below are some common applications based on different hardness levels:
- 120-140 HB (Low Hardness): Suitable for applications where high machinability is essential, such as in parts that require extensive machining, including shafts, gears, and bolts.
- 140-160 HB (Medium Hardness): Ideal for medium-duty applications that require a balance of wear resistance and strength, such as in automotive components and light machinery.
- 160-180 HB (High Hardness): Best for heavy-duty applications where wear resistance is critical, such as in industrial tools, wear-resistant parts, and high-strength structural components.
- 180-190 HB (Very High Hardness): Used in applications where the highest wear resistance is necessary, such as in cutting tools, mining machinery, and abrasive environments.
Conclusion
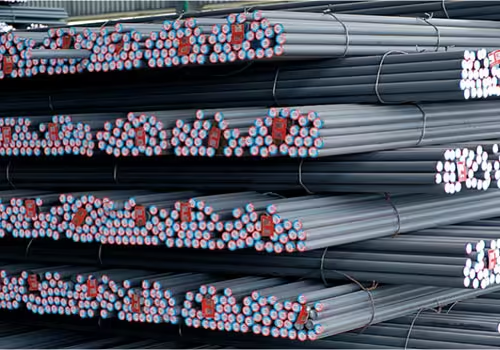
Understanding 1020 steel hardness is essential for selecting the right material for your project. Whether you need to prioritize strength, machinability, or wear resistance, the hardness of 1020 steel directly impacts its performance in various applications. By carefully considering the hardness and its effects on the material’s properties, you can ensure that your components will perform optimally in their intended environments.
Choosing the right heat treatment method can also help tailor the steel’s hardness to suit specific needs, allowing for improved durability, toughness, and resistance to wear and corrosion. Ultimately, the performance of 1020 steel is highly dependent on the balance of hardness, strength, and other mechanical properties, making it a versatile material for a wide range of industries.
FAQ
What is the hardness of 1020 steel?
The typical hardness of 1020 steel ranges from 120 to 190 HB, depending on the heat treatment process applied. This can vary based on factors such as the cooling rate and the alloying elements present in the steel.
How does increasing the hardness of 1020 steel affect its toughness?
Increasing the hardness of 1020 steel generally reduces its toughness. Harder steel is more brittle and may be prone to cracking under high impact or stress, making it less suitable for applications requiring high shock resistance.
Can 1020 steel be hardened?
Yes, 1020 steel can be hardened through various heat treatment processes, including carburizing, quenching, and tempering. These methods increase the steel’s hardness, making it more resistant to wear and tear.
What are the applications of 1020 steel with high hardness?
1020 steel with high hardness is typically used in applications where wear resistance is a priority, such as in industrial tools, gears, mining equipment, and cutting tools.
Does 1020 steel require special treatment for corrosion resistance?
While 1020 steel’s corrosion resistance is not directly related to hardness, certain heat treatments such as carburizing may enhance its ability to resist corrosion, especially in harsh environments. However, additional coatings or treatments may be necessary for environments with high corrosive potential.