
Billet Steel vs Forged: The Truth About Strength and Cost
Table of Contents
Introduction
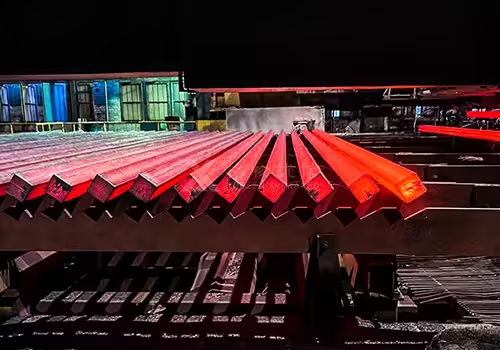
When choosing the right metal for automotive components, construction tools, or industrial machinery, one common debate surfaces time and again: billet steel vs forged. Both materials are widely used and respected in various industries due to their strength, durability, and performance. However, they have distinct manufacturing processes and mechanical characteristics that make them suitable for different applications.
Understanding the differences in strength and cost between billet steel and forged materials is essential for engineers, manufacturers, and buyers. In this blog post, we’ll explore the manufacturing techniques, physical properties, advantages, and typical uses of billet steel vs forged steel to help you make informed decisions.
What Is Billet Steel?
Billet steel is typically produced by continuous casting or extrusion of steel into long rectangular or square sections. These billets serve as the raw material for rolling, machining, or other manufacturing processes. In its raw form, billet steel has a uniform internal grain structure and is generally easy to shape and machine.
Billet steel is often favored for parts requiring intricate designs and precision cuts. It is used in sectors such as automotive, aerospace, and custom tooling. However, because billet steel is cut and shaped from a solid block rather than compressed, it may contain microvoids or weak spots if not properly inspected or processed. This is one of the key contrasts in the ongoing discussion around billet steel vs forged.
In high-performance applications, billet steel offers notable flexibility for designers who require exacting detail. Its machinability allows manufacturers to create complex geometries and custom finishes. This is particularly useful in racing applications or luxury products where aesthetic value complements functional strength.
What Is Forged Steel?
Forged steel is produced by heating steel and shaping it under high pressure. This process compresses the internal grain structure, resulting in stronger and more reliable mechanical properties. Forging aligns the grains to follow the shape of the part, enhancing directional strength and toughness.
Due to its robust strength and resistance to fatigue, forged steel is commonly used in critical components like crankshafts, axles, and connecting rods. The method may be more labor-intensive and require specialized equipment, but the outcome is a part with superior durability and load-bearing capabilities. This makes forged steel a top contender in the billet steel vs forged comparison.
Another advantage of forged steel is its resilience under extreme conditions. Whether it’s the intense forces inside an internal combustion engine or the pressure-bearing demands of industrial machinery, forged components often outlast their billet counterparts. This longevity translates to better performance and increased safety margins.
Comparing Billet Steel vs Forged: Mechanical Properties and Manufacturing
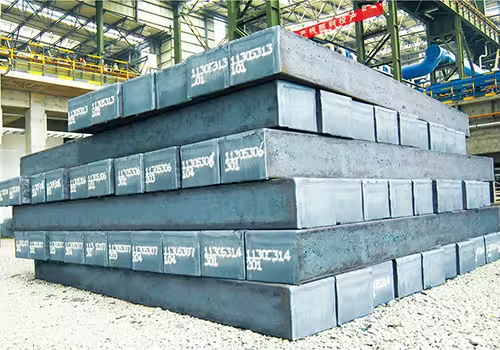
Strength and Durability
One of the most discussed aspects of billet steel vs forged is the difference in their strength. Forged steel, due to the forging process, has a tighter grain structure and better resistance to impact and stress. Billet steel, though strong, may not match forged steel in fatigue resistance unless it is specially treated or reinforced.
In terms of structural applications and components subjected to repetitive loading, forged steel stands out. The billet steel vs forged strength dynamic is clear in long-term reliability. This strength advantage explains why forged steel is so widely used in demanding industries where failure can have critical consequences.
In real-world case studies, such as aerospace and oil & gas industries, forged steel has consistently demonstrated longer service life and reduced failure rates. It’s not only about immediate load-bearing but about how the material holds up after years of exposure to vibration, pressure, and thermal cycling.
Cost Efficiency
Billet steel is generally less expensive to produce, especially in small batches or for custom pieces. Its manufacturing process is simpler and allows for precise machining. Forged steel, on the other hand, may have a higher upfront cost due to tooling and labor, but it often lasts longer in high-stress applications.
When analyzing billet steel vs forged from a cost-benefit standpoint, billet steel offers value in prototype and decorative components, while forged steel shines in lifecycle savings.
Machinability and Customization
Billet steel is ideal for projects requiring detailed shapes and intricate design features. It offers excellent machinability, which is beneficial for prototyping and low-volume manufacturing. Forged steel is harder to machine post-forging due to its density but can be custom-shaped during the forging process itself.
This comparison is one of the key advantages explored when weighing billet steel vs forged, especially for industries where design intricacy matters. For precision applications, billet steel enables tighter tolerances and superior finish quality.
Moreover, billet steel lends itself to automation and CNC processing, which is essential in industries where digital fabrication and rapid prototyping dominate. On the flip side, custom die forging offers a high degree of pre-form shaping that minimizes waste and post-processing effort.
Application Suitability
- Billet Steel: Automotive parts, bicycle frames, precision tools, and aerospace components.
- Forged Steel: Heavy-duty vehicle parts, industrial equipment, and critical structural elements.
Understanding where each material excels helps in resolving the billet steel vs forged decision in practical terms.
Comparative Table: Billet Steel vs Forged
Property | Billet Steel | Forged Steel |
---|---|---|
Manufacturing Process | Cast or extruded into billets | Heated and compressed under pressure |
Grain Structure | Uniform but random | Aligned, directional |
Strength | High | Superior |
Fatigue Resistance | Moderate to High | Excellent |
Machinability | Excellent | Moderate to Poor |
Cost | Lower initial cost | Higher initial cost, better longevity |
Best For | Precision parts, low-load applications | High-load, high-impact applications |
Why Choose Forged Over Billet (or Vice Versa)?
When comparing billet steel vs forged, the application requirements dictate the better choice. Forged steel is the preferred option for scenarios that involve high stress, impact, and fatigue due to its mechanical superiority. Billet steel, while not as durable, offers the flexibility and cost savings needed for custom or low-volume parts.
Forged steel is often seen in automotive racing, aerospace landing gear, and industrial crankshafts, where failure is not an option. These demanding environments highlight the performance superiority of forged steel.
Billet steel is common in cosmetic or non-critical parts that benefit from precision machining and aesthetic appeal. Its popularity in custom car parts and decorative applications demonstrates where billet steel vs forged favors billet.
By carefully assessing performance expectations, project timeline, and budget constraints, engineers and decision-makers can choose the most suitable material. Ultimately, the billet steel vs forged decision hinges on striking the right balance between cost-efficiency and mechanical integrity.
Common Misconceptions About Billet Steel vs Forged
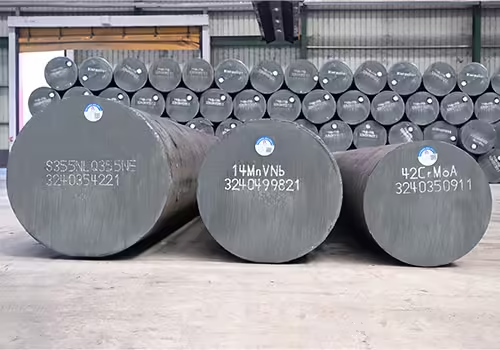
Misconception 1: Billet steel is always weaker
Not necessarily. While forged steel has better structural properties, billet steel can perform equally well in applications where the load is predictable and within tolerable limits. This is a nuance often overlooked in the billet steel vs forged debate.
Misconception 2: Forging is too expensive for most uses
Though the initial cost is higher, forged steel often reduces lifecycle costs due to fewer replacements and longer service intervals. This makes forged steel a competitive choice in the billet steel vs forged equation.
Misconception 3: Billet and forged parts look the same
Visually, parts made from either material may appear similar. The differences become evident in stress tests, long-term performance, and failure resistance. Appearance alone cannot determine the winner in billet steel vs forged comparisons.
Conclusion
Choosing between billet steel vs forged involves evaluating performance requirements, budget constraints, and intended use. Forged steel offers superior strength and fatigue resistance, making it ideal for demanding applications. Billet steel, on the other hand, provides flexibility, cost-effectiveness, and high precision, suitable for lighter or custom-use components.
Both materials have their place in engineering and manufacturing. By understanding their characteristics and comparing them effectively, you can select the best material for your specific project needs.
FAQ
What is stronger: billet steel or forged steel?
Forged steel is typically stronger due to its compressed grain structure, which improves toughness and fatigue resistance.
Is billet steel cheaper than forged steel?
Yes, billet steel is generally less expensive to produce, especially for small runs or custom machining.
Can billet steel be used in automotive parts?
Absolutely. Billet steel is used in many automotive applications where high precision and aesthetics are required.
Is forged steel harder to machine?
Yes, due to its density and strength, forged steel is often more difficult and time-consuming to machine compared to billet steel.
Which is better for high-impact use: billet steel or forged steel?
Forged steel is the better choice for high-impact or high-load scenarios due to its superior mechanical properties.