
How to Weld Acero 4140: Tips and Techniques
Introduction
Welding is an essential skill in metalworking, and understanding how to weld different materials effectively can significantly impact the success of a project. One such material that has gained popularity in various industrial applications is acero 4140. This alloy steel is known for its high strength, toughness, and wear resistance, making it ideal for applications ranging from automotive parts to machinery components. In this blog post, we will explore the best practices for welding acero 4140, including preparation, techniques, and considerations to ensure optimal results.
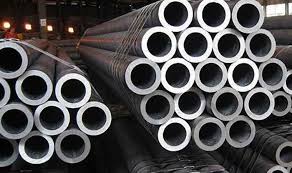
What is Acero 4140?
Acero 4140 is a low-alloy steel containing chromium and molybdenum. It is classified under the AISI/SAE 4140 standard, and its chemical composition typically includes:
Element | Percentage (%) |
---|---|
Carbon | 0.38 – 0.43 |
Manganese | 0.75 – 1.00 |
Chromium | 0.90 – 1.20 |
Molybdenum | 0.15 – 0.25 |
Phosphorus | 0.04 max |
Sulfur | 0.04 max |
This composition grants acero 4140 its unique properties, making it a versatile choice for many engineering applications.
Preparing to Weld Acero 4140
Before you begin welding, proper preparation is crucial to achieving a strong weld joint. Here are the key steps to prepare for welding acero 4140:
Clean the Material
Ensure that the surfaces to be welded are free from contaminants such as rust, oil, and paint. Use a wire brush or grinder to clean the area thoroughly. Any debris can lead to weld defects and reduce the strength of the joint.
Check the Thickness
4140 Acero comes in various thicknesses, and this will influence your welding approach. For thicker sections, preheating may be necessary to avoid cracking. Typically, preheating to around 300°F (150°C) is recommended for sections over 1 inch thick.
Select the Right Filler Material
Choosing the correct filler material is vital for welding 4140 acero . The filler metal should ideally match the properties of the base material. For 4140 acero , a low-alloy filler rod or wire is usually suitable. Consult your supplier for recommendations based on your specific application.
Welding Techniques for Acero 4140
There are several welding techniques you can employ when working with 4140 acero . Each method has its pros and cons, so it’s essential to choose the right one for your project.
Shielded Metal Arc Welding (SMAW)
SMAW, or stick welding, is one of the most common methods used for welding 4140 acero . It offers versatility and portability, making it suitable for various environments. Ensure to use an E7018 electrode, which is ideal for low-alloy steels.
Gas Metal Arc Welding (GMAW)
GMAW, or MIG welding, is another effective technique for welding 4140 acero . It provides a cleaner weld with less spatter compared to SMAW. Using a solid wire with an Argon-CO2 gas mixture is recommended for optimal results.
Gas Tungsten Arc Welding (GTAW)
GTAW, or TIG welding, is suitable for thin sections of 4140 acero . It produces high-quality, precise welds and is ideal for applications requiring clean aesthetics. However, it requires more skill and practice.
Important Considerations When Welding Acero 4140
When welding acero 4140, several factors can affect the quality of the weld. Here are some important considerations to keep in mind:
Preheating and Post-Weld Heat Treatment
Preheating is essential for reducing the risk of cracking, especially in thicker sections. After welding, a post-weld heat treatment may also be necessary to relieve stresses and restore toughness.
Controlling Heat Input
Excessive heat can lead to distortion and affect the mechanical properties of acero 4140. Maintain a consistent travel speed and adjust your amperage settings to control heat input effectively.
Avoiding Hydrogen Embrittlement
Hydrogen embrittlement can weaken the weld and lead to catastrophic failures. To mitigate this risk, ensure that your filler material is dry and use low-hydrogen electrodes.
Table: Recommended Welding Parameters for Acero 4140
Welding Process | Filler Material | Preheat Temp (°F) | Amperage Range (A) | Voltage Range (V) |
---|---|---|---|---|
SMAW | E7018 | 300 | 90 – 150 | 18 – 22 |
GMAW | ER70S-6 | 250 | 100 – 200 | 20 – 28 |
GTAW | ER70S-2 | 200 | 60 – 120 | 12 – 15 |
Common Challenges in Welding Acero 4140
Welding acero 4140 can present several challenges. Being aware of these issues can help you take preventive measures:
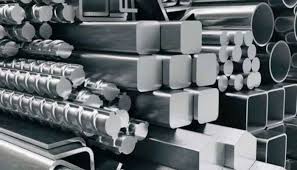
Cracking
Cracking is one of the most common issues when welding acero 4140. This can occur due to rapid cooling or improper preheating. Always monitor the cooling rate and consider post-weld heat treatments.
Distortion
Heat from welding can cause distortion in the base metal. To minimize this, use clamping methods and strategic welding sequences to control heat distribution.
Incomplete Fusion
Incomplete fusion occurs when the filler material does not properly bond with the base metal. Ensure proper penetration by adjusting your technique and travel speed.
Conclusion
Welding acero 4140 requires a solid understanding of the material properties and the right techniques to achieve optimal results. By following the tips and best practices outlined in this guide, you can overcome common challenges and produce strong, reliable welds. Always prioritize safety and quality, and don’t hesitate to consult with experienced welders or engineers when in doubt.
FAQ
What are the benefits of using acero 4140?
Acero 4140 offers excellent strength, toughness, and wear resistance, making it suitable for heavy-duty applications in various industries.
Can I weld acero 4140 without preheating?
While it’s possible, preheating is highly recommended for thicker sections to avoid cracking and ensure a strong weld.
What is the best filler material for welding acero 4140?
Low-alloy filler materials such as E7018 for SMAW and ER70S-6 for GMAW are recommended for welding acero 4140.
How can I prevent hydrogen embrittlement in my welds?
To prevent hydrogen embrittlement, ensure that your filler material is dry and consider using low-hydrogen electrodes.
Is post-weld heat treatment necessary for acero 4140?
Post-weld heat treatment is often necessary to relieve stresses and restore toughness, especially for thicker sections.
By understanding the nuances of welding acero 4140, you can enhance your projects’ quality and durability. Happy welding!