
Steel 4130 vs 4140: Which Is More Cost-Effective?
Table of Contents
Introduction
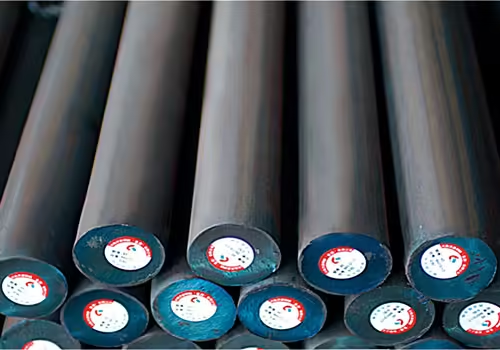

In the world of alloy steels, the comparison between steel 4130 vs 4140 is a frequent topic among engineers, manufacturers, and fabricators. Both materials belong to the chromium-molybdenum (Cr-Mo) family, offering excellent strength, toughness, and heat resistance. However, their differences in composition, mechanical properties, and cost can significantly impact project budgets and performance.
This in-depth guide explores the key distinctions between steel 4130 vs 4140, including their chemical makeup, mechanical characteristics, typical applications, and cost considerations. By the end, you’ll have a clear understanding of which alloy steel provides the best balance of performance and affordability for your specific needs.
Understanding Steel 4130 vs 4140: Composition and Properties
Chemical Composition
The primary difference between steel 4130 vs 4140 lies in their carbon content, which directly affects hardness, strength, and weldability. Below is a detailed comparison of their chemical compositions:
Element | Steel 4130 (%) | Steel 4140 (%) |
---|---|---|
Carbon (C) | 0.28-0.33 | 0.38-0.43 |
Manganese (Mn) | 0.40-0.60 | 0.75-1.00 |
Chromium (Cr) | 0.80-1.10 | 0.80-1.10 |
Molybdenum (Mo) | 0.15-0.25 | 0.15-0.25 |
Silicon (Si) | 0.15-0.35 | 0.15-0.35 |
Key Takeaways:
- Steel 4140 has a higher carbon and manganese content, making it harder and stronger.
- Steel 4130 has lower carbon levels, improving weldability and ductility.
- Both contain similar chromium and molybdenum, contributing to corrosion resistance and high-temperature strength.
Mechanical Properties Comparison
The mechanical properties of steel 4130 vs 4140 vary significantly due to their differing compositions. Below is a detailed breakdown:
Property | Steel 4130 | Steel 4140 |
---|---|---|
Tensile Strength | 560-670 MPa | 655-850 MPa |
Yield Strength | 460 MPa | 415 MPa |
Elongation (%) | 25-30% | 20-25% |
Hardness (HRC) | ~50 HRC (heat-treated) | ~60 HRC (heat-treated) |
Impact Resistance | High | Moderate |
Key Observations:
- Steel 4140 has superior tensile strength and hardness, making it ideal for high-stress applications.
- Steel 4130 offers better elongation and impact resistance, meaning it can absorb more energy before fracturing.
- Steel 4130 is easier to machine and weld, reducing fabrication costs.
Applications of Steel 4130 vs 4140

Where is Steel 4130 Commonly Used?
Due to its excellent balance of strength and weldability, steel 4130 is widely used in:
- Aerospace: Aircraft landing gear, engine mounts, and structural components.
- Automotive: Roll cages, chassis, and suspension parts.
- Oil & Gas: Drill collars, wellhead equipment, and pressure vessels.
- Bicycle Manufacturing: High-performance bike frames and components.
- General Fabrication: Structural tubing and welded assemblies.
Why Choose Steel 4130?
- Better weldability (does not require preheating in most cases).
- Easier machining (lower tool wear and faster production).
- Good toughness (resistant to cracking under dynamic loads).
Where is Steel 4140 Preferred?
Steel 4140 is favored in applications requiring extreme durability and wear resistance, such as:
- Heavy Machinery: Gears, shafts, and axles.
- Tooling & Dies: Molds, punches, and cutting tools.
- Military & Defense: Armor components and weapon parts.
- Hydraulic Systems: Pistons, cylinders, and high-pressure fittings.
- Industrial Equipment: Crankshafts, spindles, and couplings.
Why Choose Steel 4140?
- Higher hardness (better wear resistance).
- Superior strength (handles heavy loads without deformation).
- Good fatigue resistance (longer lifespan in cyclic loading conditions).
Cost Comparison: Steel 4130 vs 4140
Material Costs
When comparing steel 4130 vs 4140, pricing depends on factors like:
- Market demand (4140 is often more expensive due to higher carbon content).
- Supplier pricing (bulk orders may reduce costs).
- Form availability (round bars, sheets, tubes may vary in price).
General Price Trends:
- Steel 4130 is typically 5-15% cheaper than 4140.
- Steel 4140 costs more due to its enhanced mechanical properties.
Machining & Fabrication Costs
Beyond raw material costs, fabrication expenses play a crucial role in cost-effectiveness:
Factor | Steel 4130 | Steel 4140 |
---|---|---|
Machinability | Easier to machine | Harder, slower machining |
Tool Wear | Lower | Higher |
Welding | No preheat needed | Often requires preheating |
Heat Treatment | Optional | Usually required |
Key Takeaways:
- Steel 4130 is more cost-effective for projects requiring extensive machining or welding.
- Steel 4140 may justify its higher price in applications needing extreme durability.
Conclusion
Choosing between steel 4130 vs 4140 depends on your project’s specific needs:
- For weldability, machining ease, and moderate strength → Steel 4130 is more cost-effective.
- For extreme hardness, wear resistance, and heavy-load applications → Steel 4140 justifies its higher cost.
By carefully evaluating mechanical requirements, fabrication processes, and budget constraints, you can select the optimal alloy steel for your application.
Would you like recommendations for suppliers or further technical specifications? Let us know in the comments!
FAQ
Which is stronger, steel 4130 or 4140?
Steel 4140 is stronger due to its higher carbon content, offering better hardness and tensile strength.
Can steel 4130 replace 4140 in high-stress applications?
In some cases, yes—especially if toughness and weldability are prioritized over pure hardness.
Does steel 4140 require heat treatment?
Yes, steel 4140 typically undergoes quenching and tempering to achieve optimal hardness.
Which steel is better for welding?
Steel 4130 is easier to weld without preheating, making it more economical for welded structures.
Is steel 4140 more expensive than 4130?
Yes, due to its superior mechanical properties and additional processing requirements.