
The Pros and Cons of 4140 Alloy Steel
Table of Contents
Introduction

4140 alloy steel is one of the most commonly used materials in engineering due to its exceptional combination of strength, toughness, and wear resistance. It is often chosen for applications that require high levels of mechanical performance, such as in the automotive, aerospace, and manufacturing industries. This alloy steel is well-known for its versatility and ability to endure challenging operating conditions. However, despite its advantages, there are some potential drawbacks to using 4140 alloy steel that must be considered when making material selection decisions. In this article, we will explore the pros and cons of 4140 alloy steel in engineering and help you understand whether this material is suitable for your specific needs.
Henan Jiyuan Iron and Steel (Group) Co., Ltd. was founded in 1958. It has rich experience in production and research and development. It provides you with one-stop steel services and welcomes consultations from customers around the world.
What is 4140 Alloy Steel?
Composition of 4140 Alloy Steel
4140 alloy steel is a low alloy steel composed primarily of carbon, chromium, molybdenum, and manganese. It is classified as a medium-carbon steel that is heat-treated to improve its hardness and tensile strength. The presence of chromium and molybdenum enhances its ability to resist wear, heat, and corrosion, making it ideal for heavy-duty applications.
4140 alloy steel is available in a variety of forms, including bars, plates, and tubes. It can also be found in both normalized and quenched conditions, depending on the intended use. This alloy is often chosen for parts that must endure heavy stress, fatigue, and wear over time.
Advantages of Using 4140 Alloy Steel
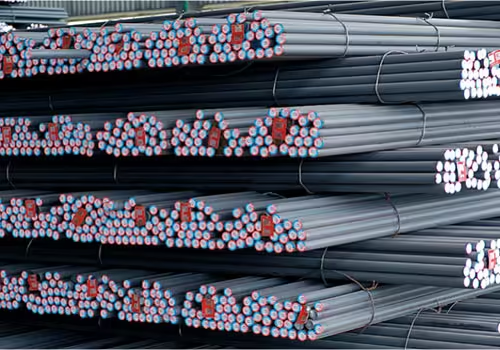
High Strength and Durability
One of the key reasons 4140 alloy steel is favored in engineering is its exceptional strength and durability. The alloy’s high carbon content provides it with superior hardness, which is crucial in applications where strength is paramount. It is particularly useful in heavy machinery, automotive components, and structural parts that must withstand high forces and stresses over long periods of time.
4140 alloy steel is known for its excellent fatigue resistance, meaning it can endure repeated loading and unloading cycles without cracking or breaking. This makes it ideal for parts that undergo continuous stress, such as axles, shafts, gears, and crankshafts. Its ability to retain strength even at high temperatures makes it a reliable material in engineering applications exposed to elevated heat.
Enhanced Toughness and Impact Resistance
Another significant advantage of alloy steel 4140 is its toughness, which refers to its ability to absorb energy and deform without fracturing. This is particularly important in applications where impact resistance is critical. The combination of chromium and molybdenum in 4140 steel improves its toughness, allowing it to perform well in environments that involve sudden or extreme forces.
For example, 4140 alloy steel is commonly used in tool manufacturing, particularly for tools subjected to high-impact conditions. It can withstand heavy loads without failing, making it an excellent choice for parts such as drill rods, punches, and dies.
Improved Wear Resistance
4140 alloy steel has excellent wear resistance properties, which means it can maintain its shape and size even after extended use in abrasive environments. This is a key characteristic for parts like gears, bearings, and shafts, which are subject to continuous friction and wear. The alloy’s resistance to wear ensures a longer service life, reducing the need for frequent replacements or maintenance.
Good Machinability and Weldability
Despite its high strength and hardness, 4140 alloy steel offers good machinability, allowing it to be easily shaped and formed using standard cutting tools. It is also known for its weldability, which is an essential factor for parts that require assembly. The alloy can be welded using various welding techniques, including gas metal arc welding (GMAW) and shielded metal arc welding (SMAW), making it versatile in different engineering applications.
Disadvantages of Using 4140 Alloy Steel
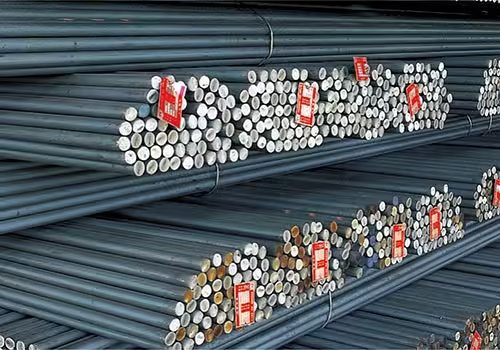
High Cost Compared to Carbon Steel
While 4140 alloy steel offers exceptional mechanical properties, it comes at a higher cost compared to standard carbon steels. The increased cost is attributed to the alloying elements used in its production, such as chromium and molybdenum, as well as the additional heat treatments that are often required. This can be a significant factor to consider for companies working on tight budgets or projects where cost is a major concern.
Susceptibility to Hydrogen Embrittlement
One of the potential drawbacks of 4140 alloy steel is its susceptibility to hydrogen embrittlement, a phenomenon that occurs when hydrogen atoms infiltrate the steel’s microstructure. This can lead to the steel becoming brittle and prone to cracking under stress. Hydrogen embrittlement is more likely to occur during processes such as welding or after exposure to certain environments, such as high-pressure hydrogen systems.
Limited Corrosion Resistance in Certain Environments
While 4140 alloy steel offers some resistance to corrosion, it is not as resistant as stainless steel or other corrosion-resistant alloys. In environments where exposure to moisture, chemicals, or salt is a concern, 4140 steel may require additional protective coatings or treatments to maintain its durability. This can increase the cost and complexity of using 4140 alloy steel in certain applications.
Requires Heat Treatment for Optimal Properties
To achieve the best mechanical properties, 4140 alloy steel often requires heat treatment, such as quenching and tempering. This process can add additional time and cost to the manufacturing process, as well as the need for specialized equipment and expertise. For applications where heat treatment is not feasible or desirable, other materials may be better suited.
Table: Properties of it
Property | Value |
---|---|
Chemical Composition | Carbon 0.38-0.43%, Chromium 0.80-1.10%, Molybdenum 0.15-0.25%, Manganese 0.60-0.90% |
Hardness (Rockwell C) | 28-32 HRC |
Tensile Strength | 850-1000 MPa |
Yield Strength | 655 MPa |
Impact Toughness | 27-35 J (at -40°C) |
Machinability Rating | 60% (relative to mild steel) |
Weldability Rating | Fair to Good |
Conclusion
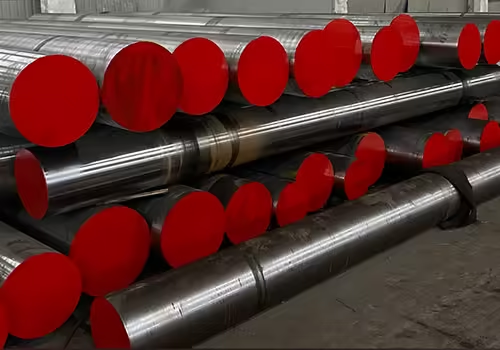
4140 alloy steel is an excellent material for a wide range of engineering applications, offering a strong combination of toughness, wear resistance, and durability. However, it does come with some limitations, such as a higher cost compared to carbon steel and potential susceptibility to hydrogen embrittlement. It is essential to carefully evaluate the specific requirements of your project and weigh the pros and cons before selecting 4140 alloy steel as your material of choice.
For applications that demand high strength, impact resistance, and toughness, 4140 alloy steel remains a reliable and versatile option. However, if corrosion resistance or cost is a major concern, it may be worth considering alternative materials. By understanding the key advantages and drawbacks of 4140 alloy steel, you can make a more informed decision on whether it is the right material for your engineering needs.
FAQ
What industries use it?
4140 alloy steel is widely used in industries such as automotive, aerospace, manufacturing, and construction. It is commonly used for parts like gears, shafts, crankshafts, and axles.
Can it be welded?
Yes, 4140 alloy steel can be welded using standard welding techniques such as gas metal arc welding and shielded metal arc welding. However, proper precautions should be taken to avoid hydrogen embrittlement during the welding process.
Is it corrosion-resistant?
While 4140 alloy steel offers some corrosion resistance, it is not as resistant as stainless steel. For applications where corrosion is a concern, additional protective coatings may be needed.
What are the main advantages of it?
The main advantages of 4140 alloy steel include its high strength, toughness, wear resistance, and good machinability. It is also versatile in various applications requiring high-performance materials.