
Top 5 Properties of 1020 Steel You Must Know
Table of Contents
Introduction
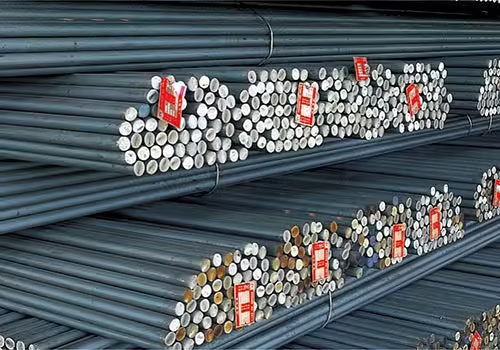
1020 steel is one of the most commonly used low-carbon steels in a wide variety of industries, including automotive, construction, and general manufacturing. Its properties of 1020 steel make it an attractive choice for many applications due to its perfect balance of strength, ease of fabrication, and cost-efficiency. This versatile material is favored for its flexibility in various forms, from sheets to rods and structural components. In this article, we will explore the properties of 1020 steel in detail, covering its malleability, weldability, strength, corrosion resistance, and affordability, all of which make it an essential material in many industrial applications.
Henan Jiyuan Iron and Steel (Group) Co., Ltd. was founded in 1958. It has rich experience in production and research and development. It provides you with one-stop steel services and welcomes consultations from customers around the world.
High Malleability and Ductility
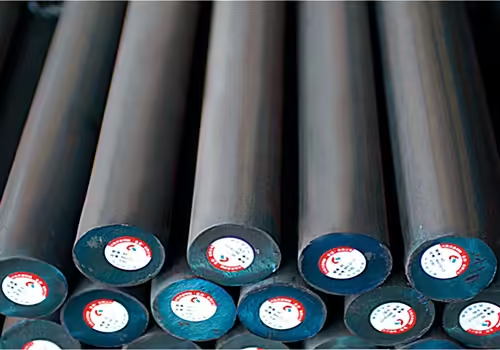
One of the most notable properties of 1020 steel is its high malleability and ductility. Malleability refers to the ability of the steel to be shaped or deformed without breaking, while ductility is its ability to stretch under stress. Because 1020 steel contains a relatively low amount of carbon, it maintains excellent flexibility, allowing it to be formed into various shapes like bars, rods, and plates without cracking or failing. These qualities make 1020 steel ideal for applications that require precise and intricate shaping or bending.
Why Malleability Matters in Steel?
Malleability is particularly crucial in industries where the steel needs to undergo heavy forming processes. For instance, it allows manufacturers to use 1020 steel for producing complex parts and components in machinery, automotive systems, and construction materials. It also makes 1020 steel a prime candidate for processes like cold working, where the material is formed at room temperature without losing its integrity.
Additionally, its ability to undergo significant plastic deformation without failure makes 1020 steel suitable for forging and casting applications where high precision and shaping are required.
Excellent Weldability and Machinability
Another significant advantage of 1020 steel is its excellent weldability. Due to its low carbon content, 1020 steel is less prone to cracking when exposed to high heat, which is common in welding processes. The material retains its properties after welding, making it ideal for use in welding applications where structural integrity is important.
In addition to weldability, 1020 steel is also known for its machinability. It’s relatively easy to cut, drill, and machine, making it a preferred choice for parts that need to be custom-made to specific dimensions. This property makes it a go-to material for industries where intricate, custom-machined parts are necessary, such as in the manufacturing of shafts, bolts, and industrial machinery components.
Applications of Weldable 1020 Steel
- Automotive: Used for car frames, axles, and other structural components that need to withstand stress while being easy to shape.
- Construction: Ideal for general structural components and heavy machinery that require welding.
- Industrial Machinery: Commonly used in parts like gears, shafts, and hydraulic components that demand both welding and precise machining.
Moderate Strength and Durability
While 1020 steel does not possess the high strength seen in alloy steels, it still provides a moderate level of tensile strength that is sufficient for many applications. With a yield strength of about 50,000 psi, 1020 steel is resistant to breaking or deforming under normal operational loads. The tensile strength typically falls between 60,000-80,000 psi, making it a durable option for many standard uses.
Its strength-to-weight ratio is particularly attractive when building machinery and structural components that need to be strong but not overly heavy. The material maintains a balance between being strong enough to withstand regular wear and tear, yet not so rigid that it becomes brittle and prone to failure.
Durability in Real-World Applications
- Machine Parts: The moderate strength and durability make 1020 steel suitable for parts like gears, shafts, and pulleys.
- General Construction: Ideal for structural applications that are not subjected to extreme stress, such as framework and secondary support structures.
- Automotive Components: Its strength is sufficient for car parts that experience regular loads but not extreme stress, like brackets and chassis components.
Corrosion Resistance
The corrosion resistance of 1020 steel is moderate, which means that while it performs well in mild environments, it is not ideal for use in highly corrosive settings. Unlike stainless steel, 1020 steel does not have a high level of resistance to oxidation and rust. However, this can be mitigated with surface treatments like galvanizing, coating, or painting, which can increase its resistance to moisture and environmental factors.
For applications in controlled environments or areas with minimal exposure to harsh chemicals or saltwater, 1020 steel remains a good choice. Additionally, it is often treated with coatings to enhance its corrosion resistance, ensuring it lasts longer in environments where moisture may be present.
Enhancing Corrosion Resistance
- Galvanizing: The process of coating 1020 steel with a layer of zinc can significantly enhance its resistance to corrosion, making it suitable for outdoor or humid environments.
- Powder Coating: A durable finish that helps protect 1020 steel from the elements while maintaining its appearance.
- Protective Coatings: Additional coatings, such as enamel or polymer, can be applied to 1020 steel to increase its resistance to rust, especially in highly corrosive areas.
Cost-Effectiveness and Availability
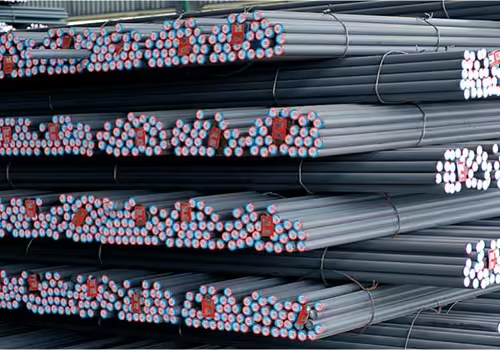
One of the most appealing aspects of 1020 steel is its cost-effectiveness. Since it is a low-carbon steel, it is much more affordable than high-alloy steels or stainless steels, making it a popular choice for manufacturers and engineers working with budget constraints. This affordability, combined with its wide availability, ensures that 1020 steel can be sourced quickly and used in various applications without breaking the budget.
It is available in a variety of shapes and sizes, including round bars, sheets, and structural forms, allowing manufacturers to select the right form for their specific needs. This availability makes 1020 steel an excellent choice for projects requiring large quantities of material, ensuring consistent quality and performance.
Why Choose 1020 Steel for Budget-Friendly Manufacturing?
Given its balance between cost and performance, 1020 steel is often the material of choice for manufacturers who need a reliable material without the high price tag associated with higher-strength or more corrosion-resistant alloys. It’s commonly used in applications where the performance requirements are moderate but still need a durable and affordable solution.
Table: Key Properties of 1020 Steel
Property | Value |
---|---|
Carbon Content | 0.18-0.23% |
Yield Strength | 50,000 psi |
Tensile Strength | 60,000-80,000 psi |
Hardness (Brinell) | 120-160 HB |
Modulus of Elasticity | 29,000 ksi |
This table highlights the key properties of 1020 steel and their typical values. It shows how 1020 steel balances strength, ductility, and cost-efficiency, making it a versatile material across various industries.
Conclusion
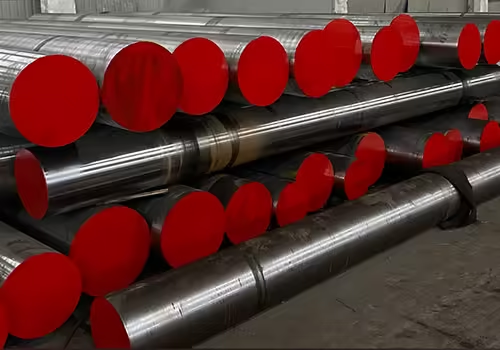
To conclude, the properties of 1020 steel provide a balanced combination of malleability, strength, machinability, and cost-effectiveness that makes it an invaluable material for a variety of industrial applications. Whether you’re working on automotive components, structural systems, or general manufacturing, 1020 steel offers a reliable and cost-efficient option that can meet moderate strength requirements without compromising on ease of fabrication.
When selecting materials for projects that require a combination of strength, flexibility, and affordability, 1020 steel proves to be an excellent choice. Its versatility and adaptability make it a staple in many industries, ensuring its continued relevance in modern manufacturing.
FAQ
What makes 1020 steel different from higher-carbon steels?
The key difference lies in the carbon content. 1020 steel has a lower carbon content compared to higher-carbon steels, which gives it better malleability and ductility but slightly less strength. This makes it ideal for applications requiring ease of forming and welding.
Is 1020 steel suitable for high-strength applications?
While 1020 steel offers moderate strength, it is not suitable for high-strength applications where heavy loads and extreme stress are involved. For such applications, higher-carbon or alloy steels are preferred.
Can I improve the corrosion resistance of 1020 steel?
Yes, corrosion resistance can be improved through processes like galvanizing, powder coating, or applying protective coatings. These treatments help 1020 steel perform better in environments prone to rust or oxidation.