
Top 6 Apps for 4140 Hardness
Table of Contents
Introduction
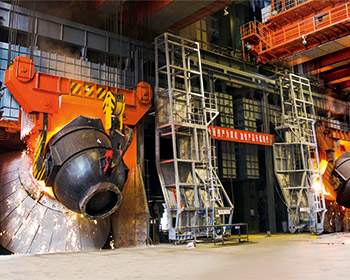
When it comes to selecting materials for demanding engineering applications, the choice of steel grade is crucial. One such steel that stands out for its versatility and strength is 4140 steel, which is often used in applications that require a particular range of hardness. The hardness of 4140 steel, known for its impressive mechanical properties, plays a significant role in determining its suitability for various industries. Understanding the importance of 4140 hardness can guide engineers and manufacturers in selecting the right material for critical applications.
In this article, we will delve into the significance of 4140 hardness and explore the top six applications where its hardness is vital for performance, durability, and safety. These industries and applications rely on the unique properties of 4140 steel, such as its hardness, to maintain high levels of performance and reliability.
Henan Jiyuan Iron and Steel (Group) Co., Ltd. was founded in 1958. It has rich experience in production and research and development. It provides you with one-stop steel services and welcomes consultations from customers around the world.
Understanding 4140 Hardness
4140 steel is an alloy that contains a mixture of carbon, chromium, molybdenum, and manganese, offering a balance between hardness, toughness, and wear resistance. The hardness of 4140 steel can be adjusted through heat treatment processes such as quenching and tempering, which enhance its mechanical properties. This process allows for the tailoring of hardness levels to meet the demands of specific applications.
The hardness of 4140 steel typically ranges between 28-32 HRC (Rockwell Hardness C scale) in its normalized state, but it can be increased to much higher levels, making it suitable for a wide variety of industrial applications. Whether in shafts, gears, or critical tooling, 4140’s hardness is integral to the material’s ability to withstand extreme conditions.
Critical Applications of 4140 Hardness
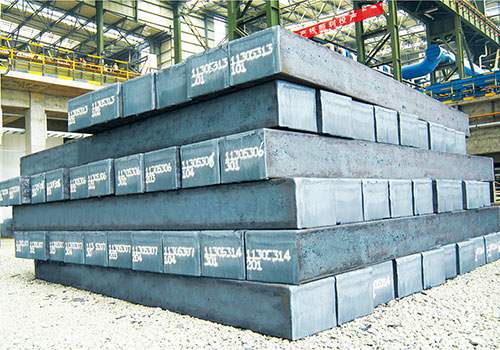
Aerospace and Aircraft Components
In the aerospace industry, components such as landing gears, turbine shafts, and structural parts undergo extreme stress and high forces during operation. The ability of these components to maintain structural integrity under such conditions is critical. Here, 4140 steel, with its custom hardness levels, is ideal for creating high-performance parts that need to endure wear, fatigue, and stress without failure.
The combination of 4140 steel’s hardness and toughness makes it a go-to choice for parts that experience cyclic loading, as well as those exposed to extreme temperatures and environmental conditions in flight. As safety is of paramount importance, the hardness of 4140 steel ensures that parts resist deformation, maintaining precise tolerances over time.
Automotive Manufacturing and Performance Parts
The automotive industry relies on 4140 steel for manufacturing various performance parts, including crankshafts, camshafts, and suspension components. In these applications, 4140 steel must maintain hardness levels to resist wear, cracking, and fatigue over long periods of use.
Crankshafts, for example, are subject to enormous stresses and pressures from the engine’s combustion process. Achieving the optimal hardness of 4140 steel ensures that the crankshaft maintains its strength and shape under extreme conditions, extending the service life of the vehicle and improving overall performance.
Heavy Machinery and Equipment
Heavy machinery and construction equipment, such as bulldozers, excavators, and mining equipment, require durable materials to withstand the harsh working environments they operate in. Components like gears, shafts, and drill bits need to maintain their hardness and resilience to resist wear and impact damage.
4140 steel is often used for manufacturing parts like these because of its excellent resistance to abrasive wear and its ability to withstand high-impact forces. The hardness of 4140 allows these parts to endure the rigors of mining, construction, and demolition without premature failure, thus reducing downtime and maintenance costs.
Oil and Gas Industry: Drill Rods and Pipe Tools
In the oil and gas industry, drilling equipment is exposed to high pressures, extreme temperatures, and abrasive materials. Drill rods, drill collars, and other downhole tools are often made from 4140 steel because of its hardness, which provides excellent resistance to wear and deformation under harsh conditions.
The hardness of 4140 ensures that these tools can penetrate tough materials such as rock and shale, maintaining their shape and functionality during deep drilling operations. Without the appropriate hardness, drill bits and rods would wear down quickly, leading to frequent replacements and costly delays.
Tooling and Die Manufacturing
4140 steel is widely used in the manufacturing of tools and dies that require high strength and wear resistance. In industries such as plastic molding, metal stamping, and die casting, tools must withstand heavy loads, abrasions, and thermal stresses.
The hardness of 4140 is critical in these applications, as it allows tools and dies to maintain their sharp edges and precise dimensions over long periods. This results in increased efficiency and a reduced need for tool maintenance, making 4140 a cost-effective material for the tooling industry.
Military and Defense Applications
For military-grade parts, including armor-piercing projectiles, tank tracks, and firearm components, material strength and hardness are crucial to ensure reliability under battlefield conditions. 4140 steel, with its hardening capacity, is often used in these demanding applications.
The high hardness of 4140 steel allows military components to resist the stresses of combat situations, such as high impact forces and explosive conditions. Its ability to retain structural integrity even under extreme circumstances makes it indispensable for the defense sector, where performance and durability are critical to operational success.
The Importance of 4140 Hardness in These Applications
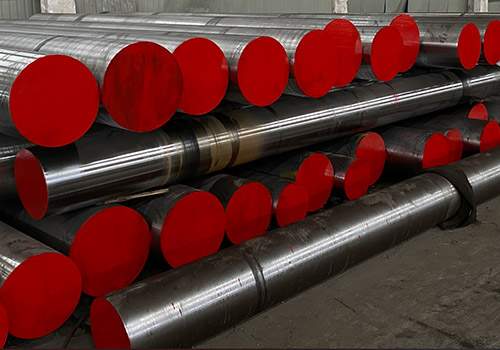
The hardness of 4140 steel directly affects its ability to withstand wear, impact, and high-stress conditions in the applications mentioned above. Whether in aerospace, automotive, oil and gas, or military applications, the right hardness ensures that components perform optimally without premature failure.
When choosing 4140 for critical parts, manufacturers need to consider the required hardness based on the expected service conditions. This ensures that the material can meet the specific demands of the application, whether that involves high wear resistance, high tensile strength, or the ability to handle high-impact forces.
Table: 4140 Hardness and Its Role in Different Applications
Application | Required Hardness Range (HRC) | Role of 4140 Hardness |
---|---|---|
Aerospace Components | 28-32 HRC | Ensures resistance to fatigue, wear, and stress under high loads |
Automotive Performance Parts | 30-35 HRC | Provides durability and wear resistance for critical engine components |
Heavy Machinery | 28-35 HRC | Ensures resistance to impact and abrasive wear in tough working conditions |
Oil and Gas Drilling Tools | 30-40 HRC | Offers strength and wear resistance for high-pressure drilling environments |
Tooling and Die Manufacturing | 32-40 HRC | Maintains sharpness and precision under heavy load and abrasion |
Military and Defense | 30-40 HRC | Provides durability and resistance to impact in high-stress environments |
Conclusion

The hardness of 4140 steel is a defining factor that determines its performance across a range of industrial applications. From aerospace to heavy machinery, the ability of 4140 to resist wear, deformation, and fatigue is essential for ensuring the reliability and longevity of critical components. Understanding the role of 4140 hardness in these industries can guide engineers and manufacturers in making informed decisions about material selection and heat treatment processes.
By tailoring the hardness of 4140 steel to the specific demands of each application, manufacturers can enhance the overall performance of their products and reduce the risk of failure in harsh conditions. As industries continue to demand higher-performance materials, 4140 steel’s unique balance of hardness and toughness remains a go-to choice for a variety of critical applications.
FAQ
What is the optimal hardness range for 4140 steel?
The optimal hardness range for 4140 steel typically falls between 28-32 HRC in its normalized state. However, depending on the application, it can be heat-treated to reach higher hardness levels, up to 40 HRC.
How does 4140 hardness affect its performance?
The hardness of 4140 steel directly impacts its resistance to wear, fatigue, and deformation under high-stress conditions. Higher hardness generally enhances wear resistance, making it ideal for applications like automotive and aerospace components.
Can 4140 steel be used in both high and low temperature environments?
Yes, 4140 steel performs well in both high and low temperature environments, provided that its hardness is optimized for the specific operational conditions.
How do manufacturers achieve the desired hardness in 4140 steel?
The desired hardness in 4140 steel is achieved through heat treatment processes such as quenching and tempering, which alter the microstructure of the steel to enhance its hardness and toughness.
What industries use 4140 steel for its hardness?
Industries that commonly use 4140 steel for its hardness include aerospace, automotive, oil and gas, heavy machinery, tooling and die manufacturing, and military and defense.