
Why 1020 Alloy Steel Is a Reliable Choice?
Table of Contents
Introduction
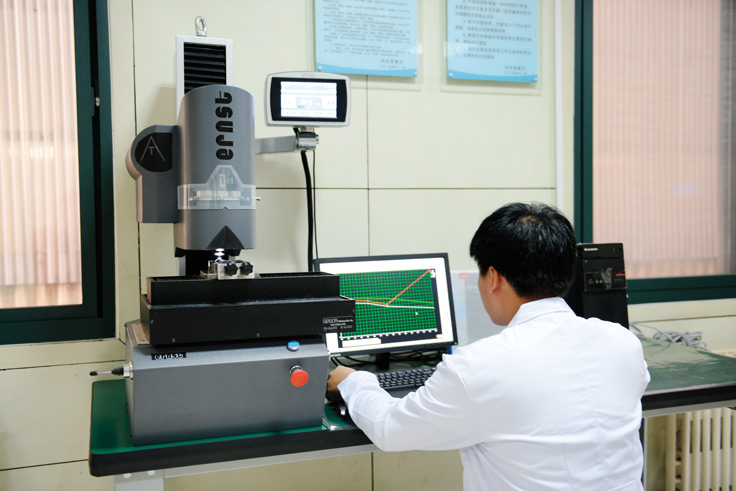
1020 alloy steel is often regarded as one of the most versatile and widely used types of low-carbon steel. With a carbon content of 0.20%, it strikes a unique balance between strength, machinability, and affordability. This makes it an ideal material for a wide range of applications, from automotive and construction components to industrial machinery and tools. In this blog post, we’ll explore the many reasons why 1020 alloy steel is such a reliable choice, examining its characteristics, uses, advantages, and how it compares to other steel alloys in terms of performance and cost-effectiveness.
Henan Jiyuan Iron and Steel (Group) Co., Ltd. was founded in 1958. It has rich experience in production and research and development. It provides you with one-stop steel services and welcomes consultations from customers around the world.
What is this?
1020 alloy steel is a low-carbon steel that falls under the AISI (American Iron and Steel Institute) 10xx series. This series of steels is characterized by its carbon content, with 1020 alloy steel specifically containing around 0.20% carbon. This relatively low carbon content means it has excellent formability and weldability, which are key attributes for many manufacturing processes. However, it does not offer the same high tensile strength or hardness as higher-carbon steels, making it ideal for applications where moderate strength is needed without the brittleness that can come with higher-carbon alloys.
Key Characteristics
- Carbon Content: At 0.20%, 1020 alloy steel has enough carbon to ensure good strength, but it is low enough to maintain high workability and weldability.
- Tensile Strength: This steel typically achieves a tensile strength of around 420 MPa, which is suitable for many general-purpose applications.
- Machinability: 1020 alloy steel is known for its excellent machinability, allowing it to be shaped and cut with relative ease during manufacturing processes like turning, milling, and drilling.
- Weldability: Due to its low carbon content, 1020 alloy steel is highly weldable and can be used in applications where components need to be joined through welding techniques.
- Cost-effectiveness: It is a cost-effective material compared to higher-carbon alloys and alloys that require more specialized production processes.
Common Applications
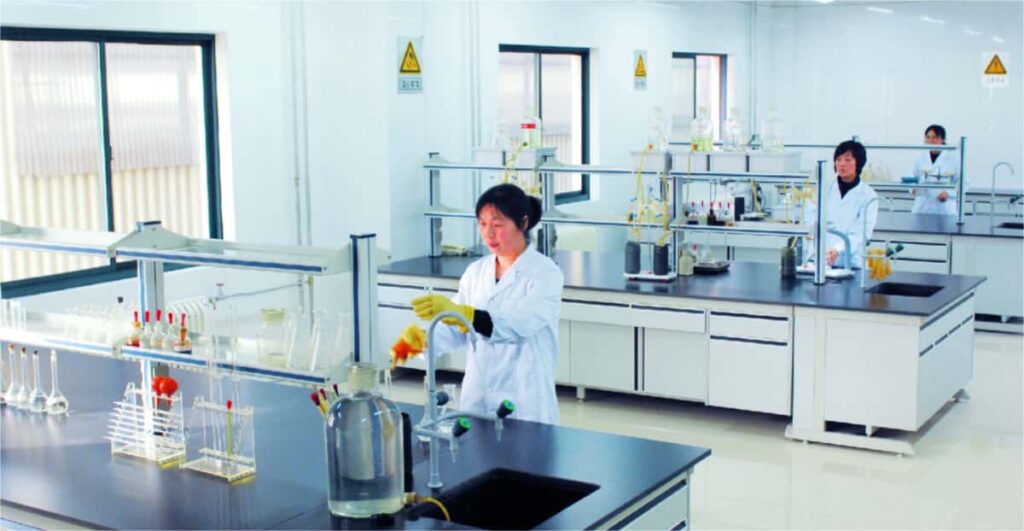
1020 alloy steel is used across a variety of industries due to its versatility and reliable performance. From the automotive sector to manufacturing and construction, this material’s combination of strength, ease of use, and affordability makes it ideal for numerous applications.
Automotive Components
In the automotive industry, 1020 alloy steel is commonly used for parts like shafts, axles, and gears. These components require moderate strength and durability to function effectively under stress but don’t need to withstand the high-impact forces seen in other more specialized components. 1020 alloy steel provides a good balance of toughness and cost-efficiency for these parts.
Machinery Parts
Many industrial machines use parts made from 1020 alloy steel, such as bearings, crankshafts, and other components that need to endure mechanical stress while still being easy to produce. Its excellent machinability and weldability make it an ideal choice for these types of machinery.
Construction Materials
In construction, 1020 alloy steel is used for structural elements where weight, strength, and flexibility are crucial. It can be found in beams, columns, and other structural supports in buildings, bridges, and other infrastructure projects. Its affordability and good weldability also make it suitable for welded structures in construction.
Industrial Tools
The material is also used for hand tools and certain types of fasteners, where moderate strength and toughness are required. Tools such as wrenches, drill bits, and fasteners benefit from the ease of machining and strength-to-weight ratio that 1020 alloy steel provides.
1020 Alloy Steel vs Other Alloy Steels
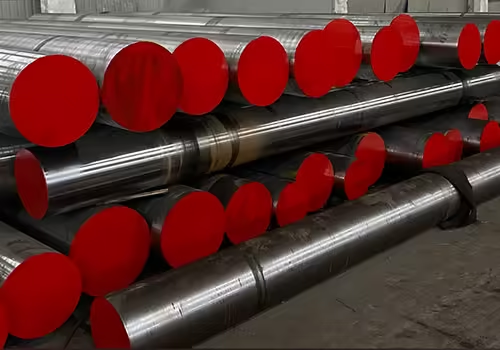
When considering alloy steels for specific applications, it’s helpful to compare 1020 alloy steel with other common alloys. While 1020 offers a unique set of benefits, it may not always be the best choice for all situations. Here’s a comparison between 1020 and a couple of other popular alloy steels: 1045 and 4140. This table highlights key differences, offering a clearer picture of where each alloy might be most useful.
Property | 1020 Alloy Steel | 1045 Alloy Steel | 4140 Alloy Steel |
---|---|---|---|
Carbon Content | 0.20% | 0.45% | 0.40% |
Tensile Strength | 420 MPa | 600 MPa | 700 MPa |
Weldability | Good | Moderate | Poor |
Machinability | Excellent | Good | Good |
Cost | Low | Moderate | High |
From the comparison, it’s clear that 1020 alloy steel offers a good balance of affordability and machinability, but it lacks the higher tensile strength of alloys like 1045 or 4140. For most applications requiring moderate strength and machinability, 1020 alloy steel is ideal, while 1045 or 4140 might be more appropriate for higher-stress conditions where stronger materials are needed.
Why Choose it?
There are several reasons why 1020 alloy steel is a go-to choice for many manufacturers, engineers, and project managers. Let’s dive into the specific reasons why it stands out.
Affordability
One of the main advantages of 1020 alloy steel is its affordability. With a relatively low carbon content and straightforward production process, it’s less expensive than many higher-carbon and alloy steels. This makes it a highly cost-effective choice for both small and large-scale manufacturing projects. If you’re working with a tight budget but still need a reliable material, 1020 alloy steel is a good option.
Ease of Machining
1020 alloy steel’s low carbon content ensures that it’s highly machinable. This means it can be easily shaped, drilled, and cut into the desired form, which reduces production times and costs. For manufacturers looking to speed up the machining process while maintaining the quality of the finished product, 1020 is an excellent choice.
Weldability
1020 alloy steel is easy to weld compared to higher-carbon steels. This is particularly important for projects where welding is required to join multiple components together. The material can be used in a variety of welding methods, including MIG, TIG, and arc welding, without compromising its overall structural integrity.
Versatility
Whether you need to create automotive components, industrial machinery parts, or structural elements, 1020 alloy steel is flexible enough to be used in a wide range of applications. It provides a balance of properties that make it suitable for both high-volume production and specialized, custom applications.
Good Strength-to-Weight Ratio
Although it doesn’t offer the highest tensile strength compared to other alloys, 1020 alloy steel provides a solid strength-to-weight ratio. This means it can perform well in many general-purpose applications where strength is required but extreme durability is not essential.
Heat Treatment
While 1020 alloy steel can be used in its as-rolled form for many applications, heat treatment is often used to alter its mechanical properties to better suit specific needs. Common heat treatments for 1020 alloy steel include:
Annealing
Annealing is a heat treatment process used to soften 1020 alloy steel, making it more suitable for machining. The steel is heated to a specific temperature and then cooled slowly, which relieves internal stresses and enhances its machinability.
Hardening
For applications that require more strength, hardening involves heating the steel to a high temperature and then quenching it rapidly in water or oil. This increases the hardness of the material, making it more resistant to wear and impact.
Tempering
Tempering is often done after hardening to reduce brittleness. By reheating the hardened steel to a lower temperature, the material becomes tougher while maintaining much of the hardness gained during the hardening process.
Conclusion
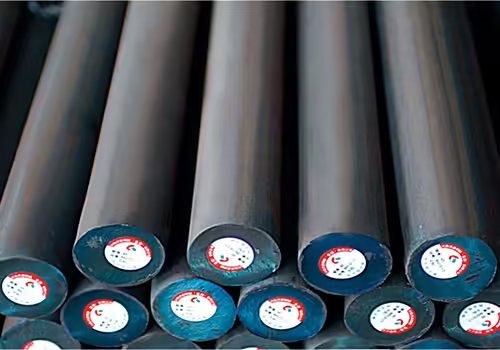
1020 alloy steel is a reliable and cost-effective material that finds use in a wide variety of industries. Its combination of affordability, machinability, and weldability makes it a versatile choice for projects ranging from automotive manufacturing to construction and machinery fabrication. Although it may not offer the extreme tensile strength of higher-carbon steels, 1020 alloy steel provides a solid balance of properties that make it a dependable choice for general-purpose applications.
FAQ
What is the primary use of 1020 alloy steel?
1020 alloy steel is commonly used in automotive parts, machinery components, and structural materials due to its excellent machinability, weldability, and overall performance in moderate-strength applications.
Can 1020 alloy steel be heat treated?
Yes, 1020 alloy steel can be heat treated using processes like annealing, hardening, and tempering to improve its mechanical properties such as hardness and tensile strength.
Is 1020 alloy steel suitable for high-stress applications?
While 1020 alloy steel offers good strength, it may not be suitable for high-stress applications where more durable alloys like 1045 or 4140 would be better choices.
How does 1020 alloy steel compare to other materials in terms of cost?
1020 alloy steel is one of the most affordable alloy steels, making it a cost-effective option for projects that require good performance but without the higher costs of stronger alloys.